Laser cutting is currently the most widely used laser processing technology in various countries. In many fields abroad, such as automobile manufacturing and machine tool manufacturing, laser cutting is used for the processing of sheet metal parts. With the continuous improvement of the beam quality of high-power lasers, the range of processing objects for laser cutting will become more extensive, including almost all metal and non-metal materials. For example, laser cutting can be used to cut complex three-dimensional parts of materials with high hardness, brittleness, and melting point, which is also the advantage of laser cutting.
Nowadays, laser cutting enterprises in Shenyang are mainly divided into two categories: one is large and medium-sized manufacturing enterprises, which produce a large number of sheets that need to be cut and cut, and have strong economic and technological strength; The other type is collectively referred to as processing stations, which specialize in undertaking laser processing business externally and do not have their own leading products. On the one hand, its existence can meet the processing needs of some small and medium-sized enterprises, and on the other hand, it plays a role in promoting and demonstrating the application of laser cutting technology in the early stage.
The key technologies of laser cutting are the integrated technology of light, machine, and electricity. The parameters of the laser beam, as well as the performance and accuracy of the machine and CNC system, directly affect the efficiency and quality of laser cutting. The precision, efficiency, and quality of laser cutting vary with different parameters, such as cutting power, speed, frequency, material thickness, and material, so the rich experience of operators is particularly important.
1.1 Main advantages of laser cutting
(1) Good cutting quality: narrow incision width (generally 0.1-0.5mm), high precision (generally hole center distance error of 0.1-0.4mm, contour size error of 0.1-0.5mm), good surface roughness of the incision (generally Ra of 12.5-25 μ m), and the incision generally does not require secondary processing for welding.
(2) Fast cutting speed, for example, using a 2kW laser power, the cutting speed of 8mm thick carbon steel is 1.6m/min; The cutting speed of stainless steel with a thickness of 2mm is 3.5m/min, with a small heat affected zone and minimal deformation.
(3) Clean, safe, and pollution-free, greatly improving the working environment for operators.
Jiangxi laser cutting belongs to non-contact optical thermal processing and is known as an "all powerful tool that never wears out". Workpieces can be tightly packed or cut in any form to fully utilize raw materials. Due to non-contact processing, the distortion of the processed parts is reduced to a lower level and the amount of wear is minimized.
In fact, laser cutting also has its shortcomings. In terms of accuracy and cutting surface roughness, laser cutting has not surpassed electrical machining, and in terms of cutting thickness, it is difficult to reach the level of flame and plasma cutting. In addition, it cannot perform molding, tapping, and folding like a turret punch press.
1.2 Comparison between laser cutting and punch press
Previously, the Sheet Metal Processing industry used traditional punching machines for stamping, but later developed into CNC turret punching machines and composite machine tools. With the progress of society, laser cutting technology has also been introduced into the metal processing industry, and has become a rapidly developing and widely used advanced processing method for sheet metal cutting in industry. According to informal statistics, China has accumulated over 500 laser cutting systems used in industrial production, accounting for approximately 2% of the world's total operating systems.
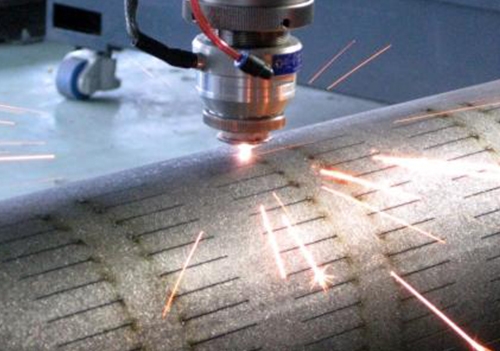
In the metal processing industry, laser cutting in Jiangxi is widely used for low carbon steel with a thickness of no more than 20mm and stainless steel with a thickness of 8mm. Most of the sheet metal parts have complex contour shapes and small batch sizes, such as automatic elevator structural parts, elevator panels, machine tool and grain machinery covers, various electrical cabinets, switch cabinets, textile machinery parts, engineering machinery structural parts, large motor silicon steel sheets, etc. In addition, some metal patterns, logos, and fonts used in decoration, advertising, and service industries can also be manufactured using laser cutting.
The CNC brick tower punching machine is suitable for mass production of products with simple shapes. The finished products include electrical cabinets, communication system exchange cabinets, elevator door panels and handrail panels, steel furniture, etc. Compared with CNC brick tower punching machines under the same cutting and stamping conditions, laser cutting machines are generally more expensive, but due to their flexibility and other advantages (such as laser cutting only needs to cut according to the drawing shape, and there is no need to manufacture molds, which shortens the production cycle). In recent years, some manufacturers have gradually realized the high efficiency it brings. In order to enhance market competitiveness, companies have purchased laser cutting machines to adapt to various types of products while owning multiple CNC brick tower punching machines. So, rather than saying that laser cutting machines compete with CNC brick tower punching machines, it is more appropriate to say that they complement each other.
2. Typical applications of laser cutting
Applications in the automotive field
Advanced 3D laser equipment can not only achieve cutting of car body parts, but also cutting, welding, heat treatment, cladding, and even 3D measurement of the entire car body, thus achieving technical requirements that cannot be achieved by conventional processing. The 3D laser equipment of Deutsche Bahn has been successfully applied for many years in companies such as Mercedes Benz, Audi, BMW, Volkswagen, General Motors, Ford, Renault, SKODA, Opel, SAAB, VOLVO, and DaimlerChrysler.
Widely used in the aviation field
Many international aviation engine companies use 3D laser equipment for cutting and drilling high-temperature alloy materials in the burner section, and have achieved success in laser cutting of aluminum alloy materials or special materials in military and civil aircraft.
The content of the article is sourced from the internet. If you have any questions, please contact me to delete it!