Firstly, CNC Machining is suitable for precision component processing in aviation, navigation, automotive, medical, industrial and other industries. CNC machining has high precision, fast efficiency, and stable quality. As the saying goes, you can do anything that flies in the air, runs on the ground, or swims in the water!
The CNC machining center adopts numerical programming, and the machining program is pre edited and entered into the CNC operating system. Processed by operators according to the process. Machine tools are also divided into ordinary CNC machining centers, 3-axis, 4-axis, 5-axis, and composite machining centers.
CNC machining centers can perform complex precision component machining with multi axis linkage, and can also be used as reference for research and development companies to produce metal or plastic prototypes.
CNC machining centers can process aluminum profiles, stainless steel, zinc alloys, acrylic, ABS, and various plastic raw materials. High compatibility. Its technology can be divided into precision turning, precision drilling, precision milling, precision grinding, grinding, and post-processing.
Precision machining and drilling: Many precision light alloy parts use this method to process workpieces (aluminum alloy or magnesium alloy), with a coordinate accuracy of up to 2 microns.
Precision milling cutter: used for machining complex shaped aluminum or beryllium alloy structural components. Based on the precision of the machine tool's guide rail and spindle, high mutual positional accuracy can be obtained. By using carefully ground diamond cutting heads for high-speed milling, the correct mirror surface can be obtained.
Precision machining and grinding: used for machining shaft or hole components. Most of these components are made of hard steel with high hardness.
Grinding: Using the principle of mutual grinding of mating components to selectively process irregular protrusions on the processed surface, the accuracy can reach 0.01mm.
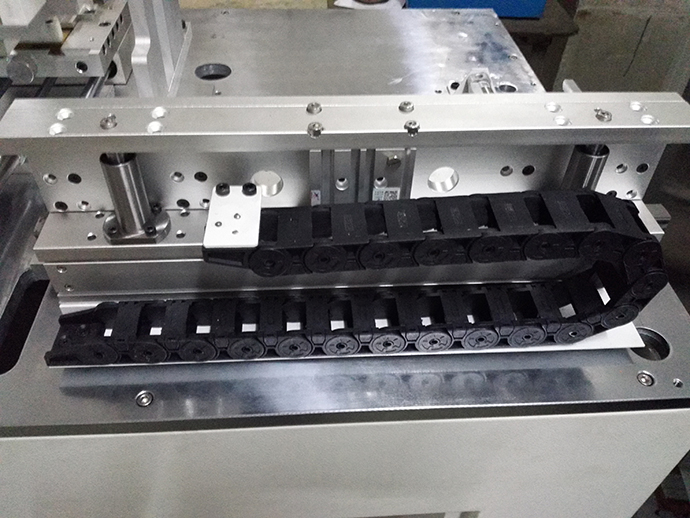