Stamping molds are essential process equipment for stamping production and are technology intensive products. The quality, production efficiency, and production cost of stamped parts are directly related to mold design and production. The unevenness of mold design and production technology is one of the important indicators to measure the unevenness of a country's product production level, which largely determines the quality, efficiency, and development ability of new products. Therefore, the stamping die frame device is also very important. Today, I will summarize the precautions for stamping die frame:
1. When installing the stamping mold device, pay attention to the flatness of the device between the mold and the stamping table on the corresponding tonnage punch according to the punching force of the mold;
2. It is necessary to clean the surface of the upper and lower, concave and convex molds of the stamping die before setting up the mold, to ensure that there are no debris on the mold that may cause scratches on the product surface. During installation, it is necessary to ensure that the stamping table of the punch press is parallel to the bottom surface of the mold slider;
3. It is necessary to check the integrity of the mold guide column, mold punch, working spring, positioning pin and other mold accessories, as well as the blade and cutting edge of the mold, to ensure that the cutting surface is flat during production. It is necessary to organize the punching holes, waste holes, etc. of the mold before setting it up to ensure that waste is discharged in a timely manner during production;
4. The mold should be placed in the center of the punch table;
5. When pressing the mold, the slider should be raised first, and then slowly lowered to the bottom dead center using the inching method; For molds with a mold handle, it is necessary to align the mold handle with the mold handle hole until it reaches the bottom dead center, and then close and shrink the mold first. For molds without handles, place the mold in the appropriate position and be careful not to block the feeding holes of molds with feeding holes;
7. The cushion block used must be flat, and its stress balance should be checked. Attention should be paid not to block the material to prevent damage to the mold caused by blockage;
8. The formable mold first tightens the upper mold, then puts in the waste material of the required punching thickness, adjusts it to the appropriate closing height using a slider, and empties it two to three times before locking the lower mold;
9. When using a V-shaped stamping mold frame, close and lock the upper and lower mold sliders, and then raise the slider to the size of the thickness of the material being punched;
10. After setting up the mold, check whether the upper and lower molds are locked, whether there are any abnormal phenomena, and finally ensure that the items are in place. Organize the site;
11. After the mold is completed, it is necessary to strictly check the dimensions of the stamped parts according to the drawing requirements before mass production can be carried out.
This article is from EMAR Mold Co., Ltd. For more EMAR related information, please click: www.sjt-ic.com,
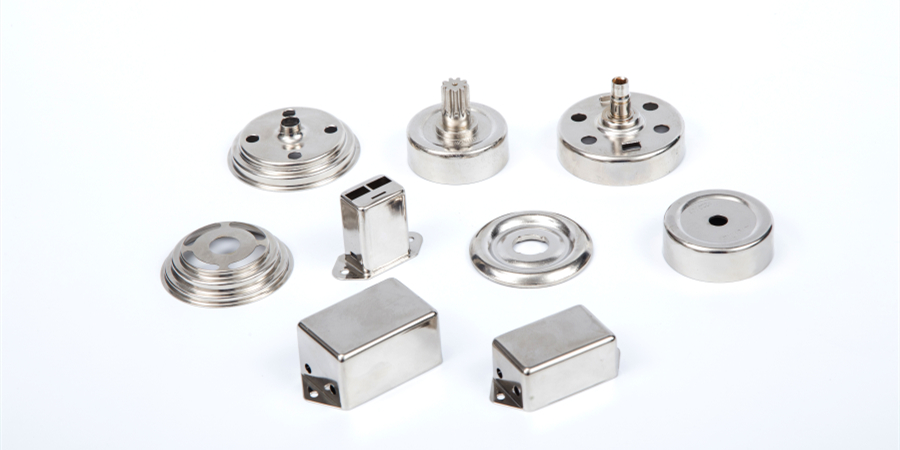