Aiming at the problem of hidden errors in digital design of sheet metal processing parts in Shenyang, this paper analyzes the errors generated in the modeling process and possible elimination measures, and analyzes the problem of error accumulation in CNC measurement. In addition, the results of the best fit between the measurement point cloud and the surface Z of the part were analyzed, and new criteria for error evaluation were proposed. Through the above measures, machining errors of parts can be reduced and the qualification rate of parts can be improved.
1. Errors and elimination methods generated when making equidistant surfaces:
We are using CATIA software to analyze with 1 When processing sheet metal parts with a thickness of 016mm, it was found that some areas had a thickness of 1.021mm, with a difference of 0.005mm. This indicates that there is an error in using the equidistant surface function to create equidistant surfaces. In order to reduce errors and achieve the required accuracy in engineering, it is first necessary to confirm that the Z-large deviation of the offset surface is within the allowable error range of the project. Secondly, when multiple offsets are required, if possible, the original surface should be used for each offset instead of the previous one.
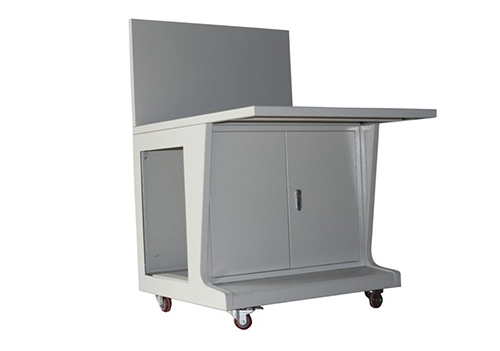
2. Errors caused by improper selection of measurement benchmarks:
For sheet metal processing parts with CNC Machining, the reserved benchmarks on top are often not design benchmarks. These benchmarks are a processed characteristic in the CNC machining process, and their error relative to the mold design benchmark is the mold machining error. After the entire mold processing is completed, due to the accumulation of tolerances, the edges, shape, etc. of the mold have an error of twice the design tolerance relative to the measurement benchmark. Assuming the external tolerance of the part is 0 25mm, mold design tolerance 0 Due to the above reasons, the size of the outer shape relative to the measurement reference has become 0.16mm, which can easily create the illusion that the measurement result is out of tolerance for the part.
To reduce errors, the measurement benchmark should be consistent with the design benchmark. In addition, when measuring the best fit between the point cloud and the surface Z of the part, recording the transformation with the least deviation can also improve the qualification rate of sheet metal processed parts.
The content of the article is sourced from the internet. If you have any questions, please contact me to delete it!