Precision Sheet Metal Processing is a processing method used to manufacture precision parts and components, commonly found in industries such as aerospace, electronics, communications, medical equipment, etc. However, in practical operation, some problems may still be encountered. This article will introduce some common problems and provide solutions.
Problem 1: Dimensional deviation exceeds requirements
In the process of precision sheet metal processing, dimensional deviations may exceed customer requirements, which may result in components not working properly or poorly fitting with other parts.
Solution:
1. Carefully analyze and evaluate the accuracy of the processing equipment to ensure that it meets the requirements.
2. Conduct simulation and testing before processing to promptly detect and correct dimensional deviations.
3. Adhere to strict quality control processes, including real-time monitoring and testing during the processing.
4. Work closely with customers, clarify size requirements, and adjust and improve processing technology in a timely manner.
Question 2: Material deformation or rupture
During the sheet metal processing, the material may deform or break, resulting in a decrease in the quality of the finished product or even rendering it unusable.
Solution:
1. Choose appropriate materials, including their hardness, strength, toughness, and other properties.
2. Proper material treatment, such as stress relief, should be carried out before processing to reduce the risk of deformation and fracture of the material.
3. Optimize the processing technology by adopting appropriate methods and sequences for punching, bending, and other processes to reduce material stress and deformation.
4. Increase mold support or adjust mold design to increase material support and stability.
5. Conduct trial production before processing to promptly detect and correct material deformation or cracking issues.
Problem 3: Poor surface quality
The surface quality requirements for precision sheet metal processing are high, and if the required indicators such as flatness and smoothness fail to meet expectations, it will affect the appearance and performance of the product.
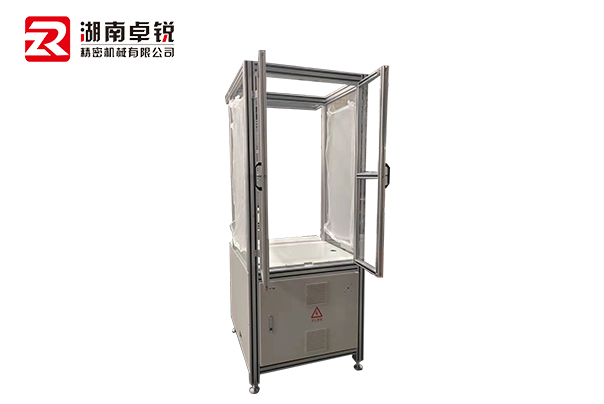
Solution:
1. Choose appropriate processing techniques and parameters, such as punch cleaning for punching machines, support methods for bending processes, etc., to ensure that surface damage is not caused during processing.
2. Proper surface treatment such as polishing, grinding, etc. should be carried out before processing to improve surface quality.
3. Strengthen the maintenance of processing equipment and cutting tools to ensure their good condition and avoid scratching or damaging the material surface.
4. Clean up waste materials in a timely manner during the processing to avoid contamination or scratching of the material surface.
5. Adopt appropriate testing methods, such as optical inspection instruments, laser scanning, etc., to conduct quality inspection on the processed products to ensure that the surface quality meets the requirements.
Problem 4: High labor cost
Precision sheet metal processing usually requires multiple processes, and each process requires time and labor costs. If the labor cost is high, it will increase the product cost.
Solution:
1. Reasonably plan and arrange processing procedures, and minimize redundant procedures and repetitive operations as much as possible.
2. Adopt advanced processing and automation equipment to improve processing efficiency and quality.
3. Train and improve employees' skills and craftsmanship, and enhance workers' operational efficiency.
4. Communicate and collaborate with customers to minimize unnecessary processing requirements and reduce product complexity.
5. Find suitable suppliers and partners to jointly reduce processing costs.
Through the above solutions, common problems in precision sheet metal processing can be effectively addressed, improving product quality and processing efficiency. Of course, different industries and products may also have specific problems and solutions that require targeted adjustments and improvements based on actual situations.