What processes are required for sheet metal shell processing? Precision Sheet Metal Processing editor to answer.
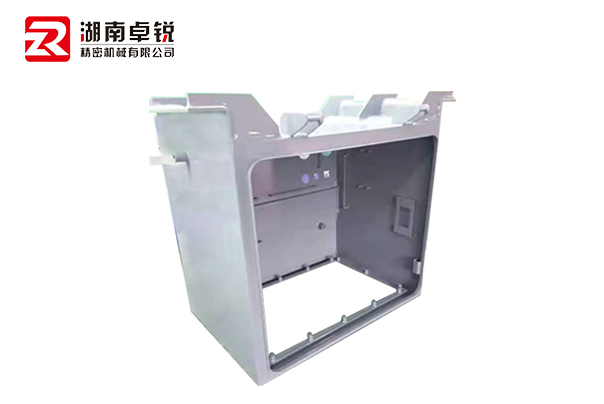
Sheet metal shell processing refers to the process of processing metal sheet into shell parts of the desired shape. Sheet metal shells are widely used in fields such as electronics, communication, automotive, and home appliances, and the corresponding processes and procedures can be selected according to the different needs and design requirements of the product. The following are common processes for sheet metal shell processing:
1. Design confirmation and material selection: Based on customer needs and product design requirements, the shell design is carried out under the guidance of engineers, and suitable materials are selected. Common sheet metal materials include cold-rolled plates, hot-rolled plates, stainless steel plates, aluminum alloy plates, etc.
2. Cutting: According to the design drawings, use cutting machines, CNC cutting machines and other equipment to cut the selected materials according to the required dimensions.
3. Bending and Forming: Use CNC bending machines, presses, and other equipment to bend and form the cut sheet metal to achieve the shape required by product design.
4. Welding: The bent sheet metal is connected through welding processes. Common welding methods include tungsten inert gas welding, pulse sheet metal welding, etc. The welding process requires attention to controlling the welding temperature and ensuring the appearance quality after welding.
5. Grinding and polishing: Polish and polish the welded shell to improve its appearance quality and smoothness.
6. Surface treatment: According to the requirements of the product, the outer shell is surface treated, such as electroplating, spraying, anodizing, etc., to increase the corrosion resistance and aesthetics of the shell.
7. Assembly: Assemble the processed shell with other related components, such as installing switches, screws, connecting wires, etc., to form a complete product.
8. Testing and quality control: By using measuring tools, coordinate measuring instruments, and appearance inspection tools and equipment, the precision and quality of the shell processing are tested and controlled.
9. Packaging and delivery: Packaging the processed shell and delivering it according to customer requirements to ensure safe transportation of the product.
The above are the general processes for sheet metal shell processing, each of which requires specialized equipment and technology, and may also require other special treatments and processes according to product requirements during the actual processing. Sheet metal processing is a highly comprehensive process that requires engineers and technicians to have rich experience and professional knowledge to ensure product quality and accuracy.