In the stamping production process, molds are an important technique that plays a very important role. In order to improve their usage level and further bring convenience to people's production and life, it is necessary to increase efforts to plan and optimize their production processes and structures. This is a primary development trend in the field of stamping mold production, and it is also an issue that relevant personnel need to pay attention to.
There are many types of structures for cold stamping dies, and it is necessary to confirm and select a reasonable die structure based on the processability and production requirements of the stamped parts during planning. The selection criteria are as follows:
1. Determine whether to use a simple die structure or a complex die structure based on the quantity of stamped parts produced. Generally speaking, simple stamping die structures have a short lifespan and low cost, while complex stamping die structures have a long lifespan and high cost. Therefore, if the number of stamped parts is not large, a simple die structure is more suitable. If there are many, a conventional die structure with a longer lifespan is more suitable.
2. Confirm the accuracy level of the stamping die based on the dimensional requirements of the stamped parts. If the dimensional accuracy and cross-sectional quality requirements of stamped parts are high, a precision die structure should be selected. For stamped parts with general accuracy requirements, a general die structure can be used. Choose the type of stamping die based on the existing equipment. For example, when deep drawing workpieces with a double action press, using a double action die structure is much better than using a single action die structure.
4. Select the type of unloading equipment in the die structure based on the thickness of the stamped sheet metal. For example, when punching workpieces with thicker plates, if the requirements for surface flatness and tip accuracy are not high, a fixed unloading equipment can be used. When there is a high requirement for the flatness of the surface of the blanking or punched parts, it is more suitable to use elastic unloading equipment.
5. Choose the type of mold based on the technical conditions and economic feasibility of the mold making process. For example, when the requirements for mold making technology are low, a relatively simple die structure should be planned as much as possible. However, when the variety of mold making equipment is complete and the processing accuracy is high, in order to increase the service life of the mold and achieve large-scale production, a more complex precision die structure should be selected.
Planners should consider multiple factors when choosing the stamping die structure method. Because both simple stamping dies and conventional stamping dies have their own advantages and limitations, it is necessary to conduct a comprehensive analysis and comparison to make the selected stamping die structure as reasonable and reliable as possible.
This article is from EMAR Mold Co., Ltd. For more EMAR related information, please click on www.sjt-ic.com,
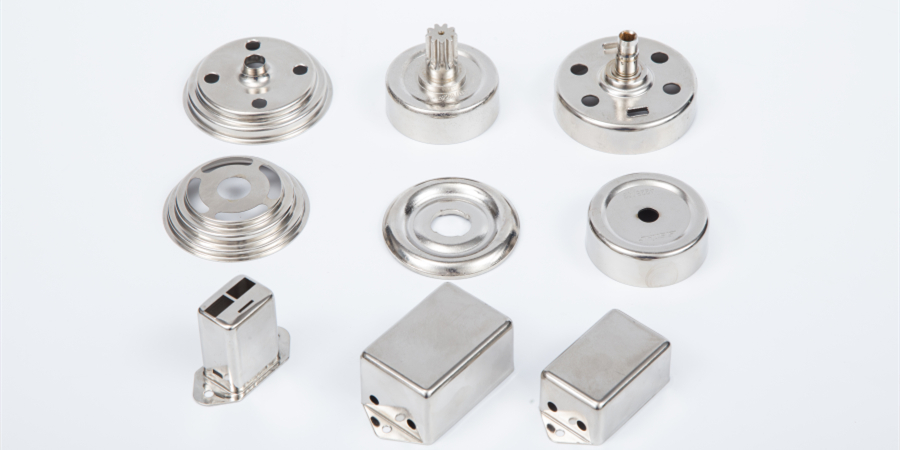