The structure of precision stamping molds directly affects the accuracy and quality of precision stamping parts. As an important carrier in the cold stamping production process, stamping molds have very common characteristics. And it is precisely because of its own characteristics that we need to consider a scientific and reasonable perspective when planning stamping dies.
Good mold planning can improve mold lifespan, durability, production power, reduce production costs, and ensure product quality. So what should we pay attention to when planning molds?
1. In mold planning, the selection of mold materials, heat treatment, and surface treatment, especially for metal deep drawn parts.
2. Material strip planning is an analysis of the product forming process, which basically determines whether the stamping die is successful.
Before planning the material strip, it is necessary to understand the service requirements of the parts, including material function, punching tonnage, punching table top, SPM (punching per minute), feeding direction, feeding height, mold thickness requirements, material utilization rate, and mold service life. When planning the material strip, CAE analysis should be conducted simultaneously, with the primary consideration being the thinning rate of the material, and more communication with the customer is necessary.
3. When testing the mold, it is necessary to slowly close the upper mold. When there is a stretching process, it is necessary to use a fuse to measure the thickness of the material position. After the gap between the material positions reaches the material thickness, try the mold again. The cutting edge must be aligned first. Please use movable inserts for the drawstring to adjust its height. The reference hole and reference surface must be stamped with the mold before placing the product on the measuring tool for measurement, or sending it to CMM for 3D presentation.
4. Red Dan must be well matched, otherwise the product will be unstable and unable to undergo later mold modification and judgment, and the part size will not meet customer requirements. For parts with many bends, the bending should be adjusted step by step according to the process when adjusting the mold.
6. When adjusting the forming viewpoint, it is possible to reduce the R angle during bending or move the line reference to achieve the goal of reaching the forming viewpoint.
7. When adjusting the mold, most people use shims to adjust the unevenness of the molded male, or move the molded male part back and forth left and right. The shims are usually made of stainless steel hard sheets.
8. Regarding the cutting edge line affected by molding, it is necessary to choose to cut it after molding, and special positions can be completed by transverse cutting.
9. Regarding multiple reference hole positions, choose the method of one-time punching to avoid affecting accuracy after step-by-step punching and cutting.
10. Regarding product rupture, various methods such as adding packaging, extruding materials, increasing the forming area of the sheet rod, and opening holes can be adopted during early stretching. CAE analysis should be conducted before mold modification.
This article is from EMAR Mold Co., Ltd. For more EMAR related information, please click on www.sjt-ic.com,
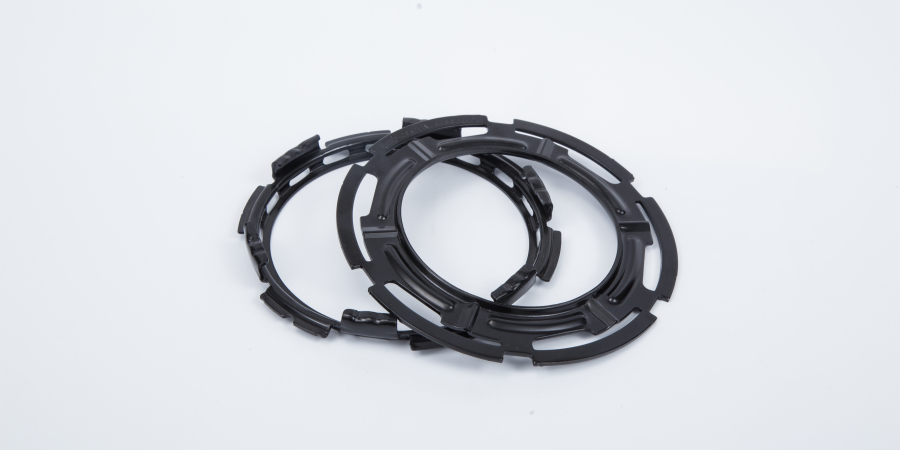