Sheet metal forming has the characteristics of flexible processing and suitability for small batch production, and is widely used in various industries such as chassis and cabinets, household appliances, and hardware products. With the acceleration of various household appliances and instrument updates, many products are produced in a miniaturized and lightweight manner. How to quickly meet the needs of various products is an urgent problem to be solved in the sheet metal forming process.
In the past, the main equipment for sheet metal forming and processing was traditional punching machines, laser cutting machines, and CNC bending machines. The disadvantage was low machining positioning accuracy, and the machining size often relied on experienced sheet metal processing operators to ensure. This was very difficult for many small and precise products, and product quality could not be guaranteed. In recent years, with the rapid development of automation, automated production lines have emerged in the public eye, greatly reducing the skill requirements for sheet metal processing operators and providing sufficient guarantees for processing products with higher precision requirements.
Sheet metal forming mainly includes three processing processes: cutting, bending, and welding. In terms of cutting, the traditional cutting method is punching and cutting, using a punch combined with a mold. Firstly, the mold cost is high. Secondly, the gap between the grinding tools is too large, and the product burrs are large, which affects the appearance of the product and has obvious limitations. By utilizing laser material cutting, the metal coil opening, leveling, and cutting are all automated, saving the cost of purchasing molds. The cutting deformation is small, the cutting seam is small and beautiful, greatly ensuring the dimensional accuracy of the processed products, making the sheet metal cutting process more precise and efficient.
In terms of bending, CNC bending machines rely heavily on manual labor. For example, a 2.5 meter metal sheet requires one skilled operator and four auxiliary operators to complete it together. Manual operation cannot guarantee the consistent bending accuracy of each sheet metal, and there are low efficiency and safety issues with manual operation. The flexible bending center solves this problem. The sheet metal relies on a pressure arm or suction cup, without the need for skilled operators. It can be bent with just one key, with fast bending speed and high workpiece consistency
In terms of welding, traditional argon arc welding causes serious environmental pollution, low welding efficiency, large deformation of the weld seam, and the appearance of the product does not meet the requirements. By using laser welding, the deformation is small and the welding effect is beautiful, which meets the appearance and quality requirements of sheet metal products. In addition, the technical requirements for welding workers are low, the operation is convenient, and it is easy to learn. Choosing robot laser welding can also achieve automated welding, and the weld seam can be tracked, meeting the requirements of batch production with high efficiency and quality.
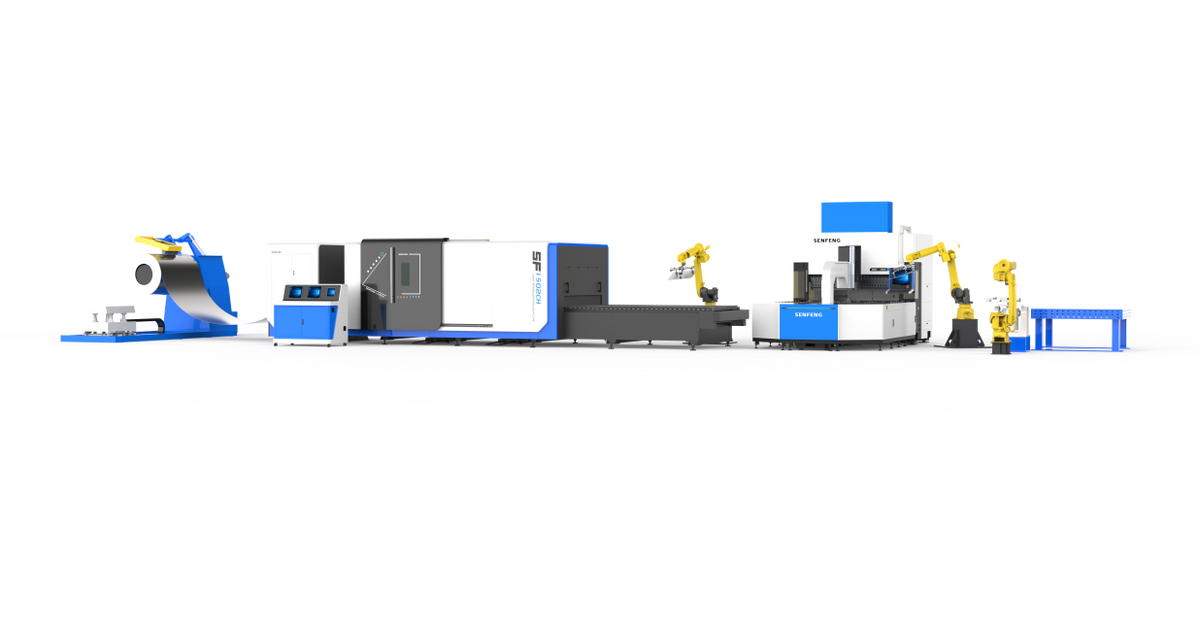
Emma Technology Co., Ltd. is one of the leading professional manufacturers of precision metal parts in China, established in 2006. It mainly undertakes business such as CNC Machining parts, metal stamping parts, and sheet metal processing.