Regarding the processing of precision parts, all materials cannot be processed with precision. Some materials with excessive hardness exceed the hardness of the processed parts, and the parts may be damaged. Therefore, these materials are not suitable for precision machining as they consist of parts made of special materials or cannot cut through elevators.
There are two types of materials for precision component processing: metallic materials and non-metallic materials.
The general metal materials with the highest hardness are stainless steel, followed by cast iron, copper, and finally aluminum. Processing of ceramics, plastics, and other non-metallic materials.
Firstly, there is a requirement for material hardness, which may be relatively high depending on the situation. However, limited to the hardness requirements of the processed parts, the material being processed is not too hard. Compared to components, it is harder and cannot be processed.
Next, the material is soft, hard, and suitable, slightly less than 1 chain of hardness compared to the components. At the same time, seeing how the processed parts are used and selecting materials reasonably for the components.
In short, precision machining has several requirements for materials, and not all materials are suitable for processing. For example, soft materials do not require processing, while hard materials cannot be processed.
Therefore, the basic one is to pay attention to the density of the material before processing. If the density is too high, it is equivalent to hardness, but the hardness exceeds the hardness of the component (rotary disc) and cannot be processed. Not only does it damage components, but it also poses dangers such as flying knives out and injuring people. Therefore, generally speaking, in mechanical processing, if the material has a lower hardness than Kata, it cannot be processed.
There are many types of mechanical processing methods, each of which requires technical requirements. According to the basic processing methods of mechanical components, attention must be paid to the following materials, bending, stretching, forming, welding, etc., all of which are mechanical processing methods.
Due to the processing methods, it is divided into general bread, counting bread, cutting disc cutting, laser packaging, and wind cutting. According to the processing method, the underground processing technology is also different. The main methods of mechanical grounding are counting bread and laser fracture. The advantage of laser fracture is that the thickness of the processed sheet is very large, the fracture speed is very fast, and the processing is very soft. The disadvantage is that it cannot be processed and formed in one go, and the online cavity parts should not be processed in this way, as the processing cost is very high.
The main welding methods used in mechanical processing factories include Yak welding, Prazma Yak welding, gas welding, pressure welding, fusion welding, Slug welding, and various additives. The welding of mechanical products mainly involves Yak welding and gas welding. Fused with softness, maneuverability, wide applicability, all position fusion can be used, the equipment is simple to use, the durability is good, the cost of bread is low, but the working intensity is high and the quality is unstable, which determines the level of the operator. The temperature and properties of gas fusion ignition can be adjusted. Compared with the Yak fusion heat source, the heat affected area is expanded, the heat is less concentrated than Yak, and the productivity is low.
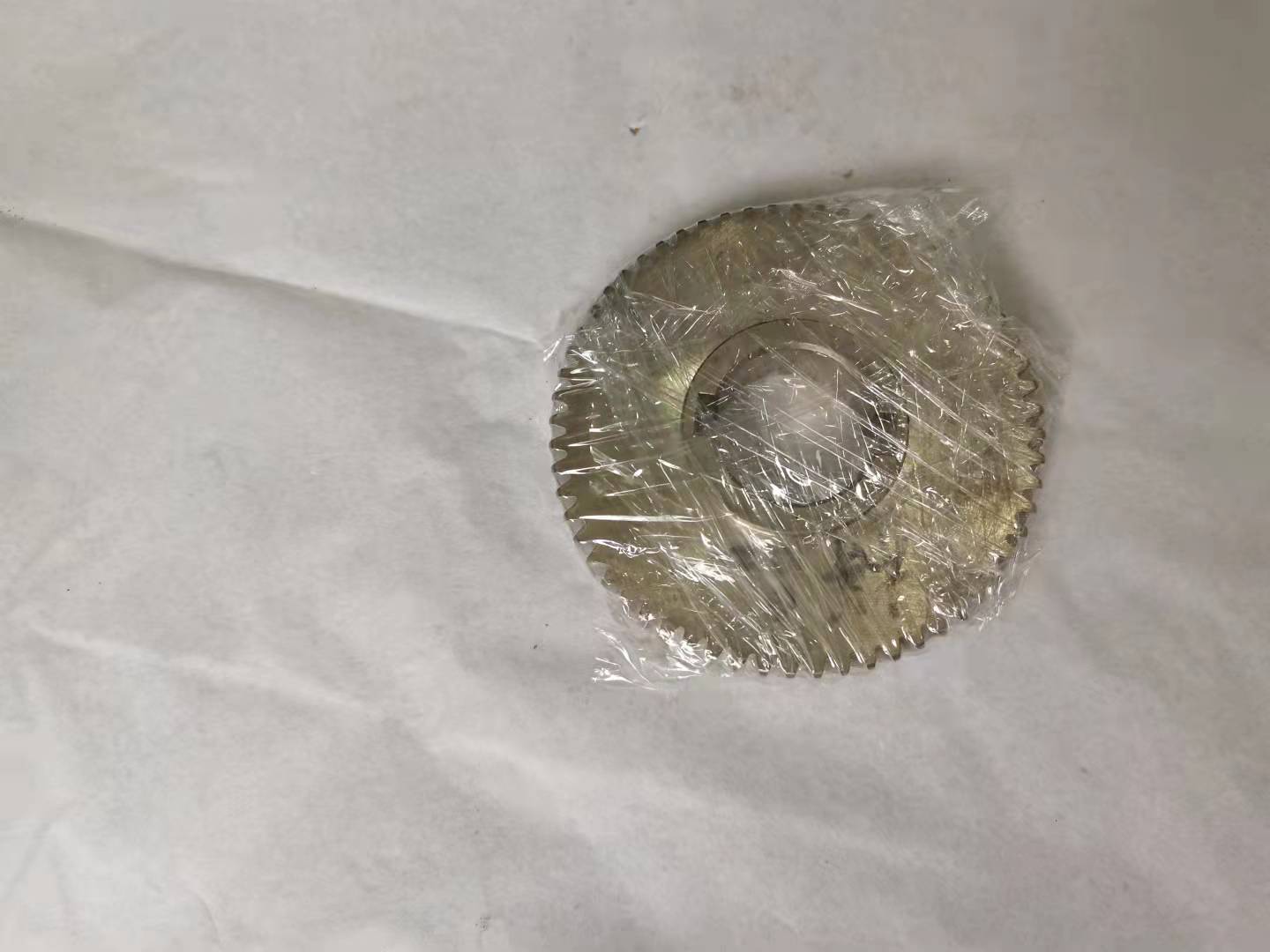