Shenzhen EMAR Precision Technology Co., Ltd. is a well-known manufacturer specializing in the external processing of high-precision CNC machine tools. It has more than 100 types of precision CNC Machining equipment. Today, let's take a look at the operation process guide for CNC machining manufacturers. This is very beneficial for standardizing the operation process and maintenance of CNC machine tools by technical personnel, including production safety, product quality stability, and equipment service life. It is recommended to save it.

1、 After the machine tool is powered on, the following precautions should be taken:
1. After the machine tool is powered on, it should first check whether all switches and buttons are normal and flexible, whether there are any abnormal situations or abnormal noises in the machine tool;
2. Check if the voltage, oil pressure, and air pressure gauge are in normal condition. If there are manually lubricated parts, manual lubrication should be performed first;
3. After the machine tool is turned on, each coordinate should be manually returned to the reference point. If an axis is already at the zero position before returning to the reference point, it must be moved to a position 100mm away from the origin before manually returning to the reference point. At this position, the machine tool should be controlled to move in the negative direction of the stroke to return to the reference point;
4. When performing worktable rotation exchange, ensure that there are no debris on the table, protective cover, or guide rail;
5. After inputting the NC program, it should be carefully proofread and ensured to be error free, including instructions, codes, values, addresses, decimal points, signs, and syntax checks;
6. Install the fixtures according to the requirements in the process specifications;
7. Accurately measure and calculate the coordinate system of the workpiece, and verify and verify the results obtained;
8. Input the workpiece coordinate system into the offset page and carefully check the coordinates, coordinate values, signs, and decimal points;
9. After inputting the offset page for tool compensation values such as length and radius, it is necessary to carefully check and verify the tool compensation number, compensation value, decimal point, positive and negative signs, etc;
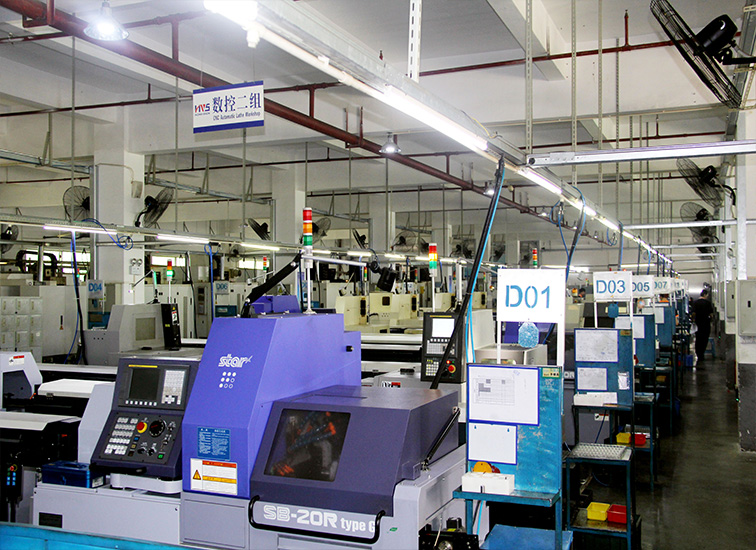
2、 During the processing of workpieces, the following precautions should be taken:
1. When performing high-precision workpiece forming processing, a micrometer should be used to detect the tool on the spindle, so that its static runout is controlled within 3um. If necessary, the tool holder system needs to be reinstalled or replaced;
2. Whether it is a part that is being processed for the first time or a part that is being repeatedly processed periodically, it is necessary to check and verify each tool and end program according to the process requirements, program, and tool adjustment card on the drawing before processing. Especially for the parts where tool length compensation and half diameter compensation are included in the program, trial cutting should be done if necessary;
3. When conducting single segment trial cutting, the metal multiplier switch should be set to a lower gear, for example;
4. When using it for the first time, it is necessary to verify whether its actual length matches the compensation value given;
5. During program execution, it is important to focus on observing the display content on the CNC system;
6. Coordinate display, which can understand the current position of the tool motion pad in the machine coordinate system and the workpiece coordinate system, understand the amount of motion in this program, and how much remaining motion is available;
7. The display of registers and buffer registers allows you to see the status of the executing program segment and also the content of the next program segment;
8. The display of the main program and subroutines can reveal the specific content of the executing program segment;
9. Dialogue display screen, which can understand the current spindle running speed of the machine tool, the current spindle cutting feed per revolution, the current cutting feed rate, the current spindle cutting load, and the stroke axis load. The spindle cutting feed per revolution is calculated to determine the cutting amount of the corresponding tool per edge;
10. During the trial cutting process, when the tool reaches a depth of 30 to 50mm on the inner surface of the workpiece, it must be verified that the remaining coordinate values of the coordinate axis are consistent with the X and Y axis coordinate values and the image while maintaining low feed rate;
11. For some special cutting tools that require trial cutting, a progressive approach is adopted to enable the data of the tool radius compensation function to be adjusted from large to small, with each trial cutting and modification;
12. During the trial cutting and machining process, after replacing the tool and auxiliary tools, it is necessary to re measure the tool length and modify the tool compensation value and tool compensation number;
13. When retrieving programs, attention should be paid to whether the position pointed by the cursor is reasonable and accurate, and whether the coordinates of the tool and machine tool movement direction are correct should be observed;
14. After modifying the program, it is necessary to carefully calculate and verify the modified parts;
15. When operating manual feed and manual continuous feed, it is necessary to check whether the selected positions of various switches are correct, clarify the positive and negative directions, identify the buttons and the set feed speed and pulse rate, and then proceed with the operation;
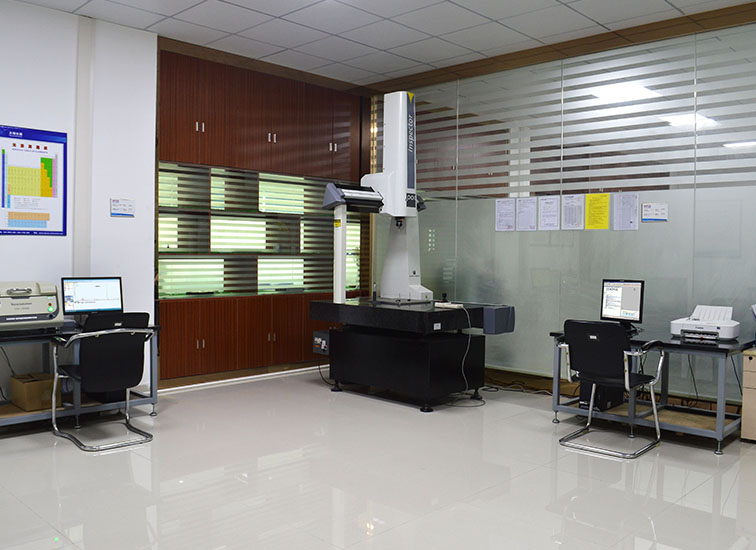
3、 After the parts are processed, the following precautions should be taken:
1. After the entire batch of parts is processed, the tool number and tool compensation value should be checked to ensure that the tool compensation value and tool number in the program, offset page, adjustment card, and process card are exactly the same. When the tool is reused, it should be re aligned on the tool presetter to effectively reduce the impact of tool wear on the processed parts;
2. Unload the tools from the tool library, clean and number them according to the adjustment card or program, and store the disks, tools, and process cards as a set;
3. After unloading the fixtures, some fixtures should be recorded for their installation position and orientation, and after recording, they should be archived;
4. Stop each coordinate axis at the middle position;
5. If you need to shut down at this time, you can press the power disconnect button on the operation panel, and then wait for a moment to allow the spindle cooling oil in the spindle to partially flow back before automatically shutting down;
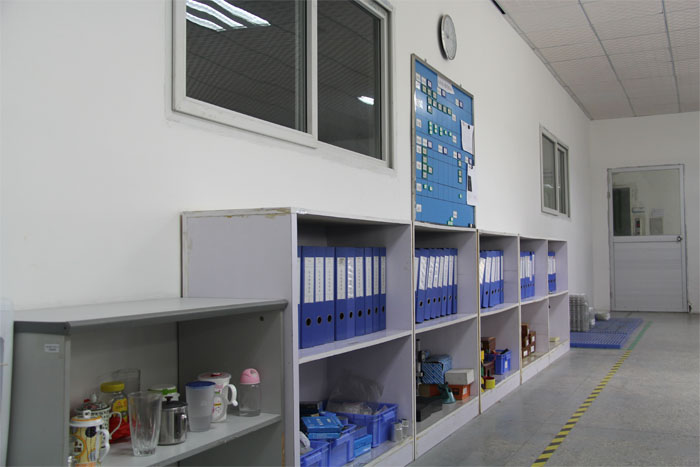
The above is a detailed explanation of the operation process manual for CNC machining manufacturers. We hope it can be helpful to you. Familiarize yourself with and master the operation manual, and strictly follow it to ensure the manual safety of machining operators, as well as the quality of product processing and the service life of machine tools. Therefore, it is necessary to be familiar with and use it well.