In the current society, with the increasing use of Sheet Metal Processing in Shenyang, the design of sheet metal parts has become an important part of the product development process. Every mechanical engineer is required to master the design skills of sheet metal parts proficiently, which enables the designed sheet metal to meet the hardware requirements of product function and appearance, as well as simplify the stamping mold production method and reduce the required cost. The characteristics of sheet metal parts include light weight, high strength, conductivity (which can be used for electromagnetic shielding), low cost, and good mass production performance. They have been widely used in fields such as electronics, communications, automotive industry, medical equipment, etc. For example, sheet metal parts are an essential component in computer cases, mobile phones, MP3 players, and audio systems.
Common problems and causes in sheet metal processing and stamping parts processing
1. Burr: During the process of punching or cutting corners, incomplete excess material is left, and burrs occur at the lower part of the steel plate cross-section. When the height of the burrs is 0.2mm or more based on the cross-section, the iron powder generated will damage the mold and cause bumps and depressions.
2. The crushing of the roll material may result in wrinkling at the edges: The guide rollers on the unwinding line may cause wrinkling when the gap between the guide rollers on the mold is small, which is caused by the roll material being fed into the non yielding balance.
3. Sliding printing: It is caused by the sliding of the roller and mostly occurs when suddenly stopping or accelerating.
4. Scratches: The primary cause of scratches on parts is sharp scratches on the mold or metal dust falling into the mold. The way to avoid scratches is to grind the scratches on the mold and remove the metal dust.
5. Convex concave: Abnormal protrusions or depressions on the surface of a material, caused by foreign objects (iron filings, dust) mixed in during the unwinding process.
6. Bottom cracking: The primary cause of bottom cracking in parts is due to poor plasticity of the material or excessive kneading of the mold edge pressing ring. To avoid this, replace the material with better plasticity or loosen the edge pressing ring.
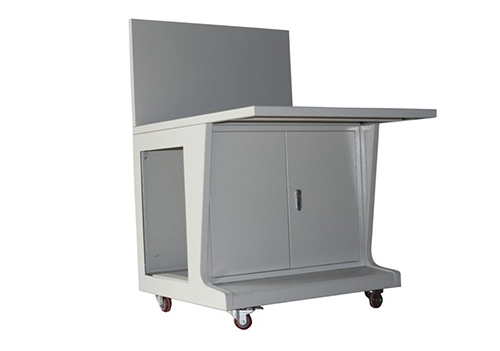
7. Roller printing: Cleaning the roller may cause foreign objects to adhere to the feeding roller (occurring at a fixed pitch), but in general, the roller printing foreign objects on the sheet can be removed.
8. Wrinkles on the side wall: The primary reason for wrinkles on the side wall of a component is due to insufficient thickness of the material (relatively small thickness is allowed to be thinner) or a slight pain during the upper and lower mold installation, resulting in a large gap on one side and a small gap on the other side. The avoidance method is to replace the material immediately or adjust the mold from scratch.
Numerical control technology is widely used in sheet metal machine tools, which solves some problems in sheet metal processing such as high precision, disorderly shape, and large batch size of parts.
CNC sheet metal machine tools include CNC shearing machines, CNC laser cutting machines, CNC punching machines, CNC bending machines, welding machines, flame cutting machines, and other machine tools. Their use in production greatly improves the sheet metal processing capability, ensuring the quality and output value of sheet metal parts, and also greatly reduces the labor intensity of workers.
Sheet metal processing is becoming increasingly intelligent due to the aforementioned technologies, and the resulting data is becoming more and more precise.
The content of the article is sourced from the internet. If you have any questions, please contact me to delete it!