The machine tool axis referred to here refers to the degrees of freedom of the machine tool, and the number of axes represents the number of degrees of freedom. For example, the usual three-axis refers to the plane motion of the worktable plus the up and down motion of the tool, while the four axis refers to the rotation of the workpiece or worktable in addition to the front three axes. In theory, the more axes there are, the higher the degree of freedom of machine tool processing, and the stronger the functionality of the machine tool. However, this does not mean that having more axes is better. There are several reasons for this.
1. Besides looking at the number of axes, we also need to consider the linkage
Whenever it comes to several axis machine tools, there is also a linkage between them. As mentioned earlier, the axis of the machine tool refers to the degree of freedom of the machine tool during machining, while the linkage of the machine tool refers to the servo axis (excluding the spindle) being able to perform interpolation simultaneously. For example, five axis five linkage refers to the coordinated movement of five motion axes during the machining of workpieces. If one or two of the five axes cannot move simultaneously with the other axes, then this machine tool is called "five axis four linkage" or "five axis three linkage". In theory, the number of axes can reach tens, dozens, or even hundreds of axes, but the linkage may not necessarily reach such a high level. This is also why five axis five linkage machine tools are considered important national equipment resources. So whenever a multi axis machine tool comes out, there are always netizens who want to emphasize linkage, because linkage can better demonstrate the performance of the machine tool in three dimensions.
2. In addition to degrees of freedom, accuracy and rigidity are also important
Machine tools refer to machines used for manufacturing machinery, with a wide variety and scope, playing a significant role in the modernization of the national economy. For different types of machining, the requirements for machine tool types and performance are also different. Therefore, although multi axis can bring higher machining freedom and functionality, many times the workpiece to be machined is not so complex, and instead requires higher precision and rigidity from the machine tool. At present, multi axis machine tools have obvious advantages in complex workpiece processing and efficiency, but there is no absolute advantage in accuracy. On the contrary, due to the complex body design, the rigidity of the machine tool is slightly weaker. In short, being suitable for processing is the best. When facing different workpieces to be processed, having more machine axes is not necessarily better.
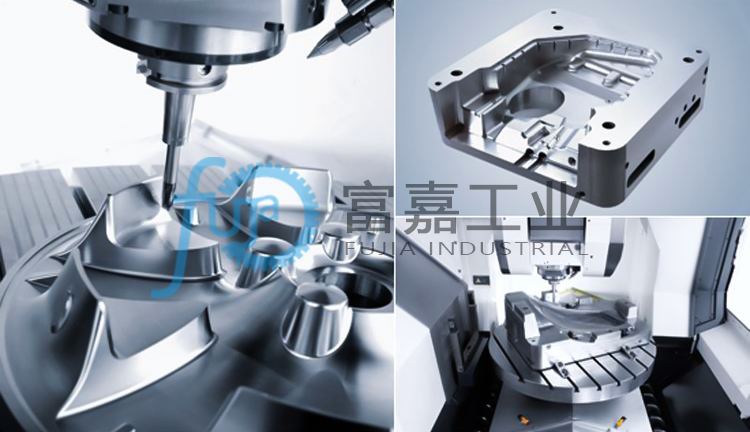
About the selection of five axis linkage machine tools
Although not all machining requires the use of five axis linkage machine tools, they do represent the high-end level of machine tools and are an effective means of solving complex machining problems such as impellers, blades, marine propellers, and heavy-duty generator rotors. With the development of manufacturing industry, the processing requirements for machine tools are becoming increasingly high, and the consumer market for five axis linkage machine tools is also expanding. So what parameters can be considered when selecting a five axis linkage machine tool? Below, the editor will briefly introduce it.
Due to the diversity of processed parts and factors such as machine speed, accuracy, and stiffness, the five axis linkage machining machine is still a specialized machine tool. Therefore, when designing and selecting a five axis linkage machine tool, the first step is to start with the processed part and typical machining trajectory, that is, to consider the characteristics of the relative motion trajectory between the tool and the part, the tool motion accuracy/speed/space, the classification of the motion axis of the five axis linkage machine tool, and the accuracy inspection.
In addition, in the design and selection of high-speed five axis linkage machine tools, the following basic principles must be followed. 1. Do the motion characteristics of the machine tool structure conform to the motion trajectory characteristics of the tool relative to the surface of the part? 2. Does the "composite motion accuracy" of the machine tool meet the requirements of tool trajectory accuracy and motion speed? 3. Does the size specification of the machine tool meet the required space for tool movement trajectory? If there are no issues with the above, then it can be basically confirmed that the selected five axis linkage machine tool meets the machining requirements.