What is the difference between Sheet Metal Processing and casting processing? Let's compare and analyze the precision sheet metal processing editor. Sheet metal shell processing
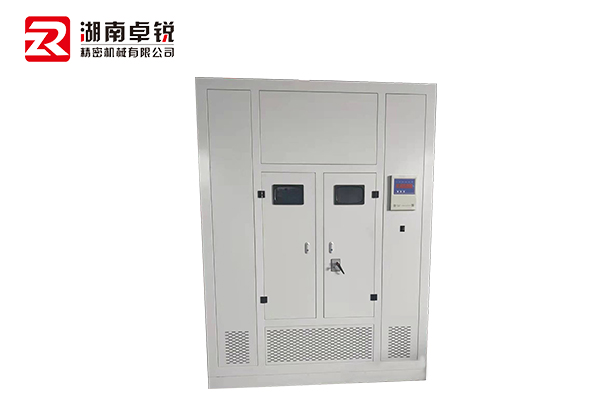
Sheet metal processing and casting processing are two different methods of metal processing. Sheet metal processing is the process of cutting, stamping, bending, welding, and other technological operations on metal sheets to produce metal products in the desired shape. Casting processing is the process of injecting molten metal or alloy into a mold to solidify it into a metal product of the desired shape.
Firstly, sheet metal processing and casting processing differ in their processing objects. Sheet metal processing mainly targets metal sheets, with a thickness generally between 0.5mm and 6mm, such as refrigerator shells, washing machine panels, etc; Casting processing is used to process metal blocks or liquid metals, and can produce larger and more complex shaped castings, such as engine cylinder blocks, car frames, etc.
Secondly, the processing techniques for sheet metal and casting are also different. Sheet metal processing generally involves cutting, stamping, bending, welding, and other processes to process metal sheets. Common sheet metal processing equipment includes shearing machines, punching machines, bending machines, welding machines, etc. For casting processing, it is necessary to first prepare a suitable mold, melt the metal or alloy, and then pour it into the mold to solidify and form it. The equipment for casting and processing includes furnaces, molds, etc.
In addition, the cost and duration of sheet metal processing and casting processing are also different. Due to the fact that sheet metal processing is mostly done manually and the process is simple, the cost is relatively low and the construction period is relatively short. However, casting processing requires the production of molds, and the process is relatively complex, so the cost is relatively high and the construction period is also relatively long.
In addition, there are differences in product performance between sheet metal processing and casting processing. Due to the use of thin metal sheets in sheet metal processing, the products are generally lighter, but their rigidity and wear resistance are relatively poor. The castings obtained from casting processing are suitable for situations where they can withstand high pressure and impact due to their thick material, good rigidity, and wear resistance.
In addition, sheet metal processing and casting processing also have certain differences in their application fields. Sheet metal processing is widely used in fields such as electronics, communications, automotive, aerospace, etc., to produce electronic casings, communication equipment, etc. Casting processing is mainly used in the fields of automobiles, machinery, construction, aerospace, etc., to produce engine cylinder blocks, automotive chassis, etc.
In summary, sheet metal processing and casting processing are two different methods of metal processing. Sheet metal processing involves cutting, stamping, bending, welding, and other process operations on metal sheets to produce metal products in the desired shape. Casting processing is the process of injecting molten metal or alloy into a mold to solidify it into a metal product of the desired shape. The two differ in terms of processing objects, processing techniques, cost and duration, product performance, and application areas.