CNC machined parts may experience scratches during the machining process due to various reasons. To avoid this situation, the following aspects can be taken into consideration: selecting appropriate cutting tools: ensuring the use of appropriate cutting tools, including tool materials, edge geometry, and cutting conditions. Choose cutting tools that match the workpiece material to reduce the risk of scratches. Control the feed and cutting speed: Adjust the feed and cutting speed appropriately to avoid excessive cutting force caused by high speed and feed amount, which can lead to scratches. Using coolant or lubricant: Using coolant or lubricant during machining can lower cutting temperature, reduce cutting force and friction, and help avoid scratches. Optimize machining path: Reasonably plan the machining path to avoid unnecessary movement and collision of the tool on the surface of the workpiece, thereby reducing the possibility of scratches. Keep the workbench and fixtures clean: Ensure that the surfaces of the workbench and fixtures are clean and free of impurities to avoid scratches caused by impurities or particles during the machining process. Regular inspection and maintenance of equipment: Regularly inspect the wear and tear of key components such as cutting tools, fixtures, and transmission systems of CNC machine tools, replace or repair them in a timely manner, and ensure the normal operation and machining accuracy of the equipment. Operating standards: Operators need to be familiar with the operating procedures and processing flow of CNC machine tools, strictly follow the requirements for operation, and avoid scratches caused by misoperation or improper operation.
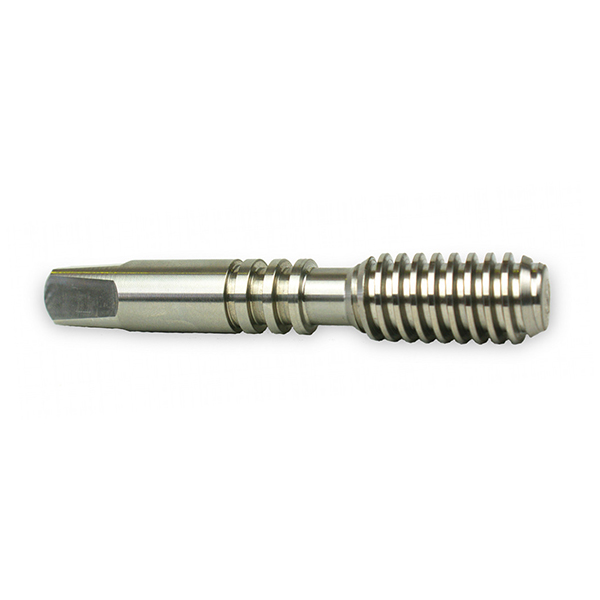