Turning is a machining method that uses cutting edges with specific shapes to rotate the workpiece. Generally, the workpiece undergoes rotational motion, while the tool of a single cutting edge moves along the machining surface. Compared with boring and milling, turning is the most common machining method in modern machining. Nowadays, the problem of turning is simply limited to the composition of chips and the cost of processing. The flow direction and chip breakage of turning chips are controllable, which not only means removing the cut material from the machining area, but also the chips need to fracture in a controlled manner and carry away the cutting heat generated by the cutting process as much as possible.
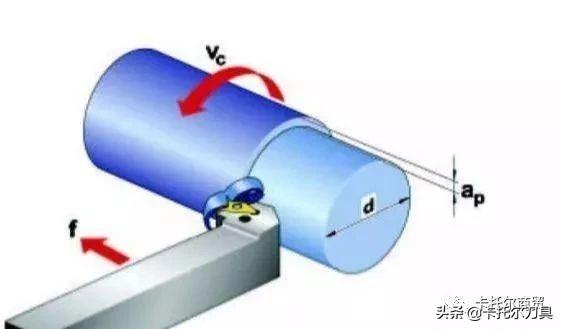
1、 Varieties of turning
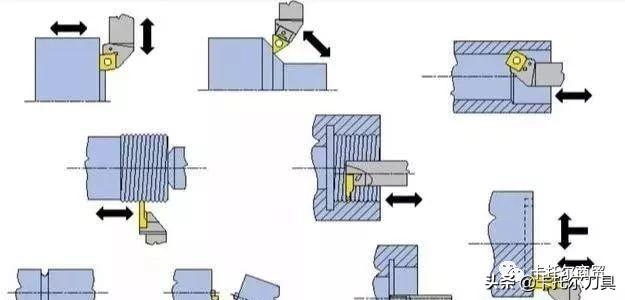
2、 Hole processing
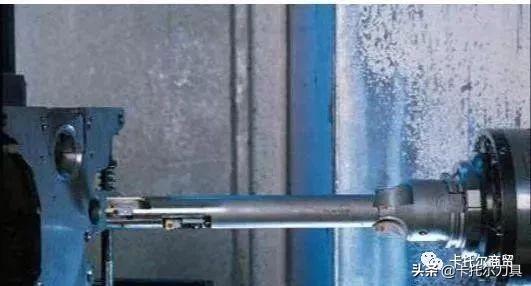
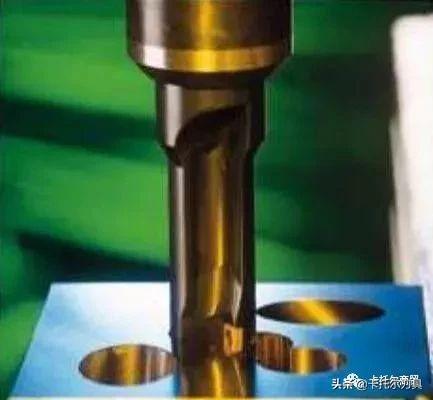
3、 Variety of hole processing
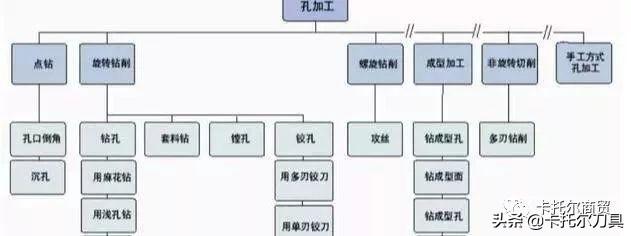
4、 Milling
Milling is also a machining method that involves graded cutting of metal through motion. The tool rotates while the general workpiece is fed in a straight line towards the tool. In some cases, the workpiece adheres to a fixed and rotating tool for lateral linear feed. Milling tools have several cutting edges that can continuously cut a certain amount of material. Two or more cutting edges cut into the material together, so that the tool cuts the material to a certain depth on the workpiece. Rough machining is marked by the amount of chips cut, and high feed and maximum cutting depth are selected during rough machining to cut as much chips as possible in a short time. Rough machining does not require high surface quality of the workpiece. During precision machining, the main consideration is the surface quality of the workpiece rather than the volume of chips. Generally, small cutting depths are used for precision machining. If you want to learn UG programming, you can obtain learning materials in QQ group 45867470. The secondary cutting edge of the tool has a special shape. According to the machine tool used, cutting methods, data, and the selected standard milling cutter, the surface quality can reach Ra1,6 µ m under excellent conditions and even reach.
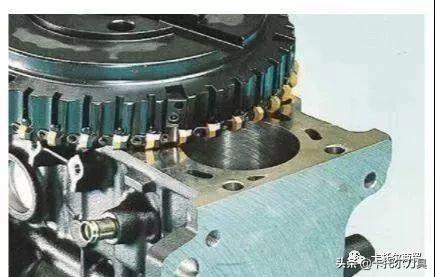
5、 Variety of milling
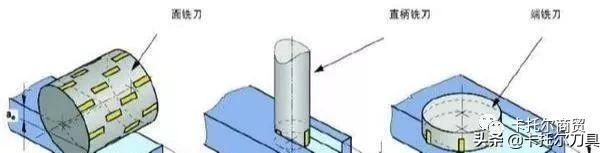

6、 Face milling
Definition: Processing plane. Face milling is the most commonly used type of milling, used for milling planes parallel to the tool face. Milling cutters are often installed on the spindle. The end face milling process can use cutting tools with a certain diameter to complete the machining of the workpiece in one stroke, and can also use milling cutters with a diameter that require several strokes to complete the machining of the workpiece.
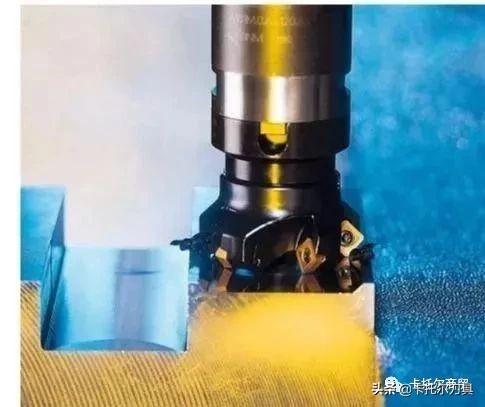
7、 End milling
Definition: Process approximately 90 step surfaces. This type of milling is somewhat similar to face milling, but the angle of the circumferential cutting edge plays a decisive role. If a certain part of the workpiece to be processed has a 90 shoulder, only this type of tool can be used. The side face (main deviation angle) of the tool is parallel to the axis of rotation. This milling is often used for step milling, shoulder milling, or end milling.
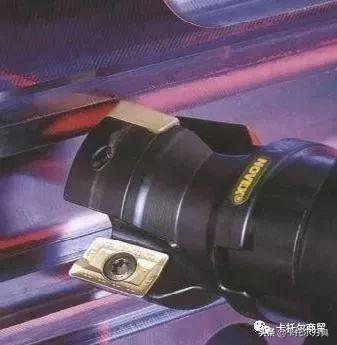
8、 Profile milling
Definition: Processing a free-form surface (curved surface)
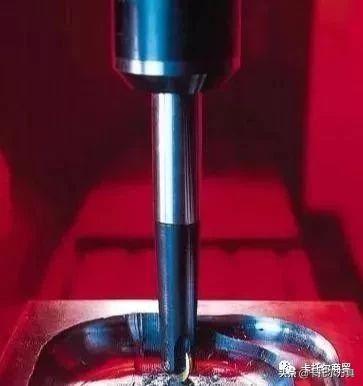
9、 Groove replacement for turning, drilling, and precision boring of indexable inserts
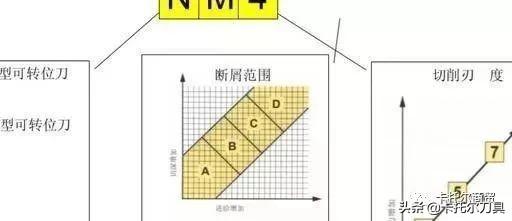
10、 Replacing the groove shape of milling indexable inserts

Suzhou Cator, also known as Suzhou Cator Trading Co., Ltd., was established in 2000. It is a trading company specializing in importing metal cutting tools and machine tool fixtures.
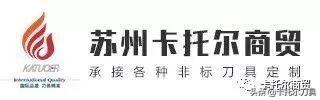
At the beginning of its establishment, it successively obtained first level agents in China for products from Kyocera, TOSG, OSG, MITSUBISHI MATERIALS, YAMAWA, and SUMITOMO.
Buddy, after reading this article, do you think it makes sense? Or do you have any other different opinions? Welcome to comment below and enjoy your own opinions and comments! You can also forward it to your social circle to see how their views are?