Time flies, it‘s already the dog days of summer, and in the blink of an eye, half of the year has passed. Summer is a busy season, and everyone is tirelessly striving for their goals and striving for this bountiful autumn. Nowadays, transportation is convenient, and airplanes, high-speed trains, and high-speed routes are integrated into major provinces and cities in China. Many users are more inclined to conduct on-site inspections when choosing CNC processing manufacturers. In fact, conducting on-site inspections of factories is very beneficial for cooperation between both parties, as it allows for the exchange of technology and the description of needs. The benefits of on-site inspections also include the following:
1. Processing capability
Many receptionists and business personnel tend to exaggerate the company‘s various strengths when communicating and exchanging with customers from other places. If they do not conduct on-site inspections to see the company‘s machine tool equipment, quality control and frequency of use, the number of skilled processing equipment, the preferred areas, the products they specialize in, the tolerance range of machinable parts, the on-site environment, and whether the inspection tools are reasonable and effective, it will be difficult to control the later orders, and even cause some troublesome consequences. Many processing manufacturers advertise well, but in reality, trading companies and workshop style companies are rampant, and material control, quality control, and efficiency control are not in place, misleading users;
2. Quality control capability
After product delivery, especially in some special industries such as aerospace, medical equipment, automotive, etc., if the processing manufacturer does not have sufficient precision inspection equipment and quality team, how can the product be judged to be qualified? If users conduct on-site inspections, they can bring these questions to the site and even communicate with on-site personnel to verify the accuracy of equipment use and inspection methods, whether the product process conversion on site is reasonable, whether the factory inspection records and packaging box transportation methods meet the standards, etc; For example, our EMAR Precision Technology has established a professional quality control team and is equipped with ultra precision inspection equipment, such as Rohs spectrometers, coordinate measuring machines, projectors, surface roughness detectors, and other devices. We can conduct high-precision testing on the material elements, performance, accuracy, and other aspects of the product to ensure that it meets the user‘s requirements after leaving the factory;
3. Process exchange
The production of technology reflects the technical capabilities of a processing company. Good processing technology and process division can effectively ensure the accuracy and performance requirements of the machine tool and the processed parts. Therefore, a good process team plays a very important role in reducing costs and completing delivery for the enterprise. After exchanging technology, technical personnel from both sides can determine the details of product materials, processing methods, delivery cycles, delivery methods, and many other aspects. After exchanging opinions, cooperation can be further achieved. If the process requirements are not met, or even if the other company does not have a process team, it may cause misjudgment for users, production capacity, and quality awareness. If the product is handed over to the supplier for processing, it may be difficult in the later stage; If a small problem occurs in these links, the company will lose credibility with customers, causing unnecessary trouble and leaving a bad impression. In severe cases, it may even face subsequent problems such as breach of contract compensation.
If there is no quality, everything is negative: production equals negative, marketing equals negative, advertising and branding equals negative, revenue and reputation equals negative. From this, it can be seen that the quality comes from production, and in terms of production, it comes from equipment, personnel, materials, methods, environment. Users need to take these issues into consideration when evaluating suppliers. For suppliers, understanding our requirements clearly will make future cooperation more convenient and enjoyable. Apply this knowledge to work, strictly control the quality, and deliver high-quality products that customers can trust and satisfy.
Shenzhen EMAR Precision Technology Co., Ltd. was established in 2001 and is located in Tangwei Industrial Park, Guangming New District, Shenzhen, at the forefront of reform. After years of development, the company is currently equipped with more than 100 precision equipment such as walking CNC lathes, cutting CNC lathes, turning milling composite machining centers, and vertical CNC Machining centers. The company has a first-class engineering team and technical processing team, as well as a first-class quality control team and advanced testing facilities. Its products cover a wide range of fields and have many years of experience in processing medical, optical, optoelectronic, and automation equipment parts. The company has successfully passed the IATF16949: 2016 quality management certification in the automotive field and strictly follows relevant standards to enter the processing sequence of automotive parts, We are one of the few manufacturers in Shenzhen with automotive parts processing qualifications. Please feel free to call us and we will provide you with professional and comprehensive product solutions.
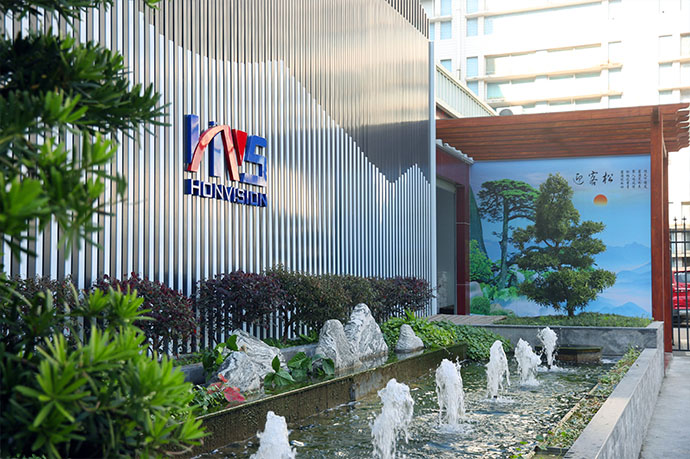