Among all the factors causing mold failure, the material and heat treatment of the mold account for about 70% of the total, becoming the main factors affecting the lifespan of the mold. Therefore, when planning the entire manufacturing process of molds, the selection of mold materials and the appropriateness of heat treatment processes are particularly important for stamping factories.
Due to the different operating conditions of various stamping molds, there are also differences in the requirements for the materials of the parts used in mold operations.
1. Requirements for punching die materials
For the working parts of thin plate punching molds, high wear resistance and hardness are required, while for thick plate punching molds, in addition to high wear resistance and compressive yield point, high fracture resistance, high bending strength, and resistance are also required to avoid mold fracture or blade breakage. Requirements for Deep Drawing Die Materials
The material of the mold operation parts is required to have outstanding anti adhesion (anti bite), high wear resistance and hardness, certain strong resistance, and good cutting processing function, and minimal deformation during heat treatment.
3. Requirements for Cold Extrusion Mold Materials
Mold operation parts are required to have high strength and hardness, high wear resistance, and a certain degree of resistance to avoid impact breakage. Due to the significant temperature increase during compression, it should also have a certain degree of heat fatigue resistance and thermal hardening.
Reasonably selecting mold materials and implementing the correct heat treatment process based on the requirements of stamping mold operation parts is the key to ensuring the service life of the mold. For molds with different purposes, stamping processing plants can summarize and consider factors such as their operating conditions, stress conditions, the function of the processed material, production batch size, and production rate, and focus on the various functions required above, and then make selections for steel grades and heat treatment processes.
This article is from EMAR Mold Co., Ltd. For more EMAR related information, please click: www.sjt-ic.com,
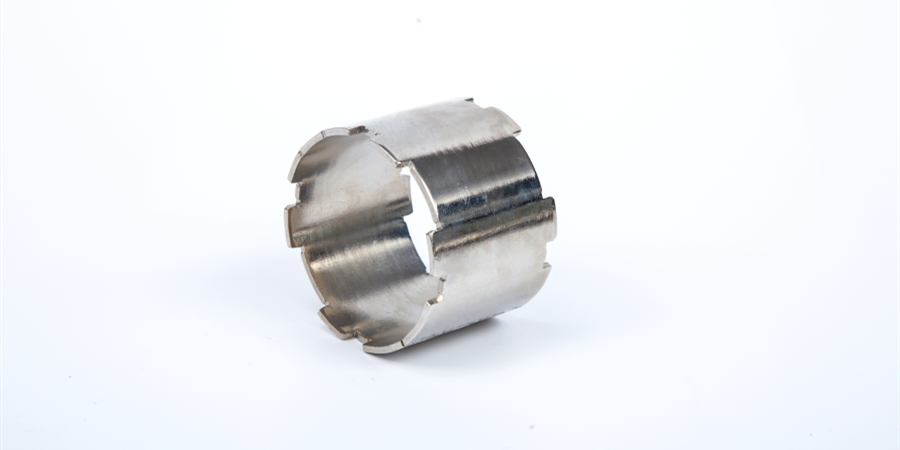