Many times, stamping factories will produce more products as inventory to prevent urgent orders requested by customers. But we often find that after a period of time, these products stored as inventory may experience corrosion due to various reasons. Therefore, it is necessary to carry out anti-corrosion treatment during the production process of Metal Stamping parts, which can effectively avoid corrosion during use after storage for a while. There are six main methods:
1. Preheating the stamped parts before spraying asphalt paint coating can improve the adhesion of asphalt paint and accelerate drying;
2. Adding a special coating to the cement mortar lining can improve the corrosion resistance of the stamping part lining;
3. The epoxy coal tar coating on metal stamping parts is a two-component coating with high adhesion and a very smooth surface; Due to the difficulty of manufacturing process and high cost, epoxy ceramic lining has certain limitations in use by stamping processing plants. However, it has high adhesion and smoothness, making it an excellent anti-corrosion coating for stamping parts;
5. Aluminate cement coating or sulfate cement coating, both of which are suitable for internal anti-corrosion of stamped parts and improve their ability to resist corrosion;
6. Polyurethane coating is a new type of green special coating developed to meet environmental protection requirements, which has good wear resistance and corrosion resistance.
This article is from EMAR Mold Co., Ltd. For more EMAR related information, please click: www.sjt-ic.com,
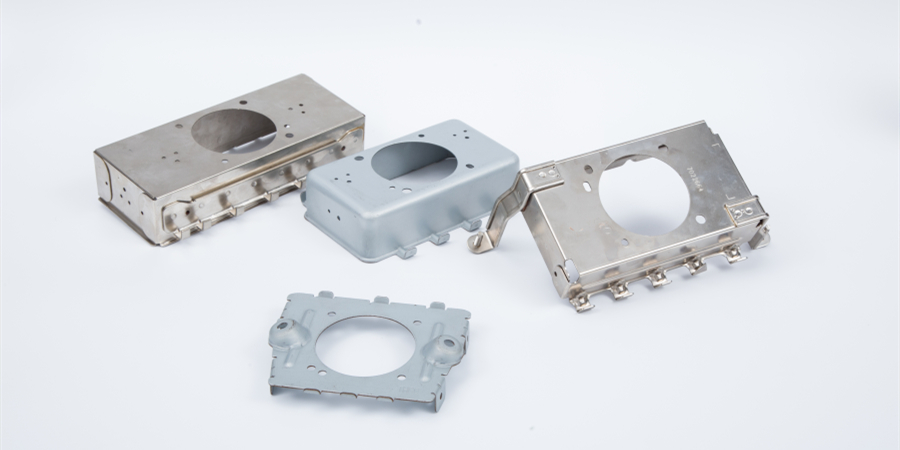