Sheet Metal Processing of vehicle body materials has also evolved from ordinary alloy steel materials to stainless steel and aluminum alloy profiles. The change in materials has driven the improvement of processing technology, and advanced technologies such as laser cutting and laser welding have been introduced into the manufacturing production lines of railway vehicles. The process of car body production is as follows: first, the purchased aluminum alloy raw materials are cut according to size using laser, water cutting and other processes, and then processed and welded into different components. These components are combined and finally welded into a car body. About 20% -30% of the steel structural components of locomotives are irregular parts, especially for parts such as locomotive driver‘s cab and body auxiliary devices, which are more suitable for laser cutting. Laser cutting realizes flexible processing, and the cutting process is easy to control and automate, which can greatly shorten the production cycle and reduce manufacturing costs, and improve product quality. Therefore, laser cutting has replaced traditional processing methods and become the main means of cutting metal sheets in the domestic and international rail vehicle manufacturing industry.
There are more and more outdoor electronic devices, many of which are specialized functional products with relatively strong targeting. Moreover, the future demands of the public include the microstructure of electronic devices, lightweight product quality, thin product wall thickness, and miniaturization of instrument housings. And these electronic equipment instruments rely on the surface protection of the instrument shell. For increasingly high-end electronic and mechanical products, the smaller the volume and lighter the weight of the shell, the stronger the portability of these instrument shells, and the more common their applicability in modern life. Moreover, these increasingly miniaturized shells are very convenient for consumer carrying and easy to maintain.
The stainless steel chassis cabinet shell manufacturer uses flexible polishing tools and abrasive particles or other polishing media to polish the surface of the stainless steel chassis cabinet. Polishing cannot improve the dimensional accuracy or geometric accuracy of stainless steel chassis and cabinets, but is aimed at obtaining a smooth surface or mirror gloss, and sometimes used to eliminate gloss (extinction). Usually, polishing wheels are used as polishing tools. Polishing wheels are generally made of multiple layers of canvas, felt, or leather, clamped on both sides with metal circular plates, and coated with a polishing agent uniformly mixed with micro abrasive powder and grease on the rim.
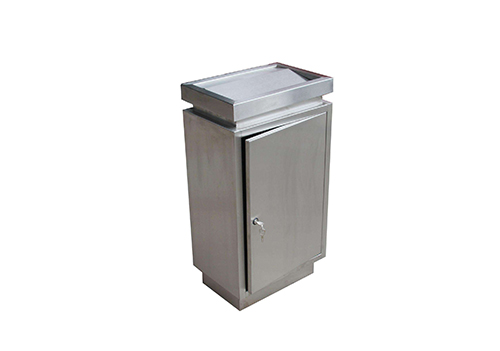