Sheet Metal Processing is a key technology that sheet metal technicians need to master, and it is also an important process for forming sheet metal products. It includes traditional methods and process parameters such as cutting, punching, and bending forming, as well as various cold stamping die structures and process parameters, equipment working principles and operating methods, and new stamping technologies and processes.
Sheet metal processing is called sheet metal processing. For example, using sheet metal to make chimneys, iron drums, oil tanks and pots, ventilation ducts, elbow heads, sky gardens, funnel-shaped structures, etc., the main processes are cutting, bending edges, bending forming, welding, riveting, etc., which require a certain amount of geometric knowledge. Sheet metal parts are thin metal parts that can be processed through stamping, bending, stretching, and other methods. A general definition is parts with constant thickness during the processing
Correspondingly, cold working of metal for castings, forged parts, machined parts, etc. usually refers to the cutting of metal, that is, using cutting tools to remove excess metal layers from the metal material (blank) or workpiece, so as to obtain a certain shape, dimensional accuracy, and surface roughness of the workpiece. Such as turning, drilling, milling, planing, grinding, pulling, etc. In metalworking, corresponding to hot working, cold working refers to the processing technology that causes plastic deformation of metal below the recrystallization temperature, such as cold rolling, cold drawing, cold forging, stamping, cold extrusion, etc. Cold working has high deformation resistance, and while forming the metal, work hardening can be used to improve the hardness and strength of the workpiece, but it will reduce plasticity. Cold processing is suitable for processing metal parts with small cross-sectional dimensions and high requirements for processing size and surface roughness.
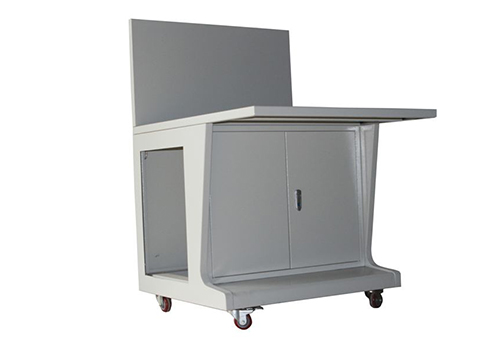