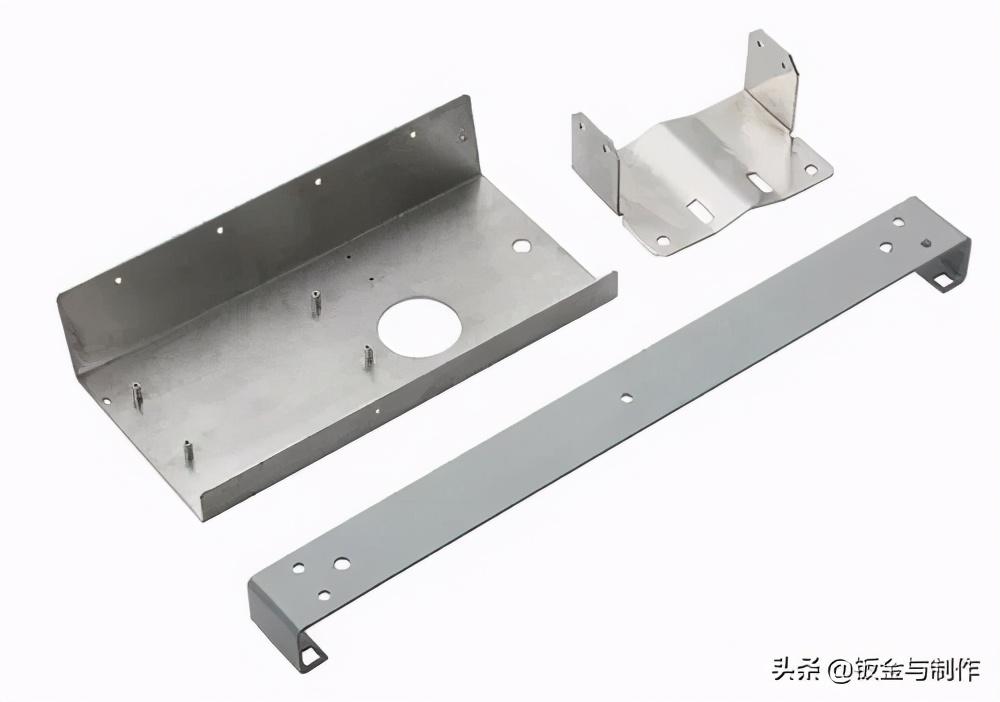
In order to meet market demand, improve labor efficiency, increase employee income, and enhance company efficiency, based on the principles of distribution according to work, more work, more benefits, efficiency priority, and fairness, combined with the actual situation of the company, this rule is formulated. Purpose: To reward employees with good performance and encourage everyone to work harder and in a better way.
1、 Applicable objects
CNC punching machine, CNC bending processing.
2、 Basic content
1. The workshop supervisor should allocate work tasks reasonably and impartially based on the difficulty level of product processing content, equipment condition, and the actual operational level of operators. At the same time, they should explain quality priorities and processing precautions to operators.
2. Operators shall be constrained in their attendance according to daily and monthly work schedules to complete the production quantity assigned by the workshop supervisor.
3. For excess (relative to other teams, relative to production tasks) completed, settlement will be made in the form of performance-based pay, with no upper limit and encouragement for more work.
Performance based salary calculation method:
1. The unit price of CNC punching machine per hour is 13.00 yuan.
2. The unit price for CNC bending is 13.50 yuan per hour.
3. Convert the daily excess into working hours and implement monthly accumulation.
4. Monthly performance-based salary=accumulated working hours * unit price per hour.
3、 Workpiece quality
1. All mold debugging must use the same test plate for bending debugging. After completing the first workpiece, it must be confirmed by the superior and quality inspection personnel, and signed as qualified before processing. During the processing, the operator needs to perform corresponding inspection actions at a frequency of every 20 batches.
2. Samples that have been signed and confirmed by quality inspectors need to be placed separately, and any quality defects that occur during processing are the responsibility of the operator.
3. After each batch of workpieces is completed, they are submitted for quality inspection. After passing the inspection by the quality inspection personnel, they can sign and confirm on the report. After signing their name and date, the report is the settlement voucher for performance, and it is submitted to the supervisor at the end of the day's work. After the material registration is returned daily, it is submitted to the management department for review, audit, and the management department will audit and calculate the salary.
4. The compensation can only be settled after the quality of the workpiece is determined to be qualified through testing.
5. Products that fail the inspection shall be handled according to different situations:
(1) If the workpiece is found to be unqualified and needs to be repaired, the operator shall be responsible for the repair, and the cost of repair shall be borne by the operator. The completion time shall not be settled.
(2) 2% of the workpieces that cannot be repaired can be considered as normal wear and tear. For workpieces that are scrapped during repair and processing, compensation shall be made based on the material cost of the workpieces according to the principle of scrapping compensation. (If the first piece is confirmed as good by the signature of the quality inspection personnel, the amount of defective products and their scrapping caused by improper operator operation and inaccurate inspection points in mass production shall be borne by the operator. If the first piece is signed by the inspector and is a defective product, the amount of defective product scrapping shall be borne by both the quality inspection personnel and the operator.). Based on the scrap form issued by the sheet metal workshop, signed by the quality inspection personnel and confirmed by the supervisors at all levels, the statistics personnel will summarize and submit it to the management department at the end of the month. The operator and quality inspection personnel will compensate for the amount and deduct it from their monthly salary.
(3) For products that fail quality inspection, a limit of 5 yuan per batch shall be applied. The quality inspector shall indicate NG or to be repaired in the report and issue a non-conforming product disposal form. After being summarized by the statistical personnel, it shall be deducted from the monthly performance salary of the operator.
(4) The operator is not responsible for any defects or scrapping caused by errors in the process drawings.
(5) For products returned by the next process or customers due to batch defects, the quality inspection department shall bear 50% of the repair or scrapping responsibility, and the economic responsibility for compensation shall be borne by the producer. The producer shall bear 50% of the repair or scrapping responsibility, and the economic responsibility for compensation shall be borne. For repaired workpieces, the parties involved or the person in charge of bending shall be responsible for repair, and the repair hours shall be settled. The two units mentioned above shall be responsible. For batch defects scrapped, the full compensation for scrapping amounts less than or equal to 1000 yuan, 50% of the compensation for raw materials greater than 1000 but less than 4000 yuan, and the production unit shall propose the scrapping amount and penalty for those exceeding 4000 yuan. The company shall decide the penalty amount.
(6) Traceable defective products shall be borne by the parties involved, and the amount of repair and scrapping shall be compensated in a certain proportion. For products that are not traceable, the amount of repair and scrapping shall be shared equally by the performance based personnel and deducted from the monthly settlement.
(7) A certain amount of normal loss is allowed for different batches of products without deducting any fees.
4、 Implementation Responsibility
1. Workshop staff and operators must comply with existing production management rules and regulations. In order to promote performance-based pay and ensure its implementation, they should each perform their own duties and duties according to their respective requirements, while also ensuring the 7S of their work area and implementing safe, civilized, and clean production.
2. Operators operate and process according to technical requirements such as production reports, calibrated workpiece content, inherent quality, and work instructions.
3. The production report should have neat and clear handwriting, be used properly, and the transmitted work data should not be altered. If it is changed due to reasons, it must have the signature date of the person who changed it, otherwise it is invalid. Operators must truthfully fill out production reports. For fraudulent personnel, a penalty of 100 yuan per occurrence will be imposed, and the piece rate salary for the day will not be calculated. Repeated offenders will be given double penalties and their performance qualifications will be revoked.
4. Newly hired employees shall be paid according to the determined hourly wage amount and attendance regulations; After the three-month probationary period expires and passes the assessment, performance will be implemented according to regulations.
5、 Salary guarantee
The efficiency has greatly improved after performance. In the production situation where sheet metal orders are saturated, the bending processing speed cannot keep up with the production efficiency of CNC punching and shearing machines. Therefore, CNC punching may appear in a state of waiting for work. Therefore, based on the technical level of CNC punching, a guaranteed salary will be issued.
Performance personnel can only receive guaranteed salary when their production cannot keep up with the processing speed, and they must firmly comply with workshop management arrangements.
2. Performance personnel who are assigned to other workshops for assistance and overtime due to less work in this workshop will be paid based on their guaranteed salary plus their overtime pay (as an auxiliary worker).
3. In the production process, for personnel who engage in fraud, slack off, and do not cooperate with production, the minimum salary will be cancelled.
4. Minimum salary payment standard:
a. Experienced in CNC punching, capable of processing various parts, and prioritizing difficult sample products. Resolutely obeying superior management with a guaranteed salary of 2500 yuan.
b. Having some experience in CNC punching, proficient in processing various parts of the company, actively cooperating with work, with a guaranteed salary of 2300 yuan.
c. Those who have grown up in our company and have some experience in CNC punching, and have worked in CNC punching for less than a year, have a guaranteed salary of 2000 yuan.
6、 For the production of sample products, as it is a new product that requires higher technical skills from operators, corresponding salary compensation will be given based on the difficulty level and the attitude of employees towards work. For those who work seriously, the salary compensation will be equal to that of the sampling personnel and the performance personnel of the day. If two machines sample at the same time, the performance salary of the previous day will be used as the benchmark.
7、 Rewards
1. Full attendance bonus of 100 yuan, excluding sick leave, marriage leave, and funeral leave;
2. Employee performance-based pay is equal to the unit price of working hours multiplied by the excess quantity plus the overtime bonus:
3. In order to encourage more work, more pay, and widen the gap in performance-based pay, the company will once again reward employees who exceed their working hours:
1) Employees who have accumulated 227-239 working hours in the current month will receive a bonus of 100 yuan each time;
2) Employees who have accumulated 239-251 working hours in the current month will receive a bonus of 300 yuan each time;
3) Employees who have accumulated 251 or more working hours in the current month will receive a bonus of 600 yuan each time;
4) Employees are only allowed to take 2 days off, exceeding which is considered as absenteeism, except for temporary overtime arrangements.