Sheet Metal Processing is called sheet metal processing. For example, using sheet metal to make chimneys, iron drums, oil tanks and pots, ventilation ducts, elbow heads, round corners, funnel-shaped structures, etc. The main processes include cutting, bending edges, bending forming, welding, riveting, etc., which require a certain amount of knowledge.
Sheet metal parts are thin metal parts that can be processed through stamping, bending, stretching, and other methods. A general definition is parts with constant thickness during the processing. The materials commonly used for sheet metal processing skills include cold-rolled sheet (SPCC), hot-rolled sheet (SHCC), galvanized sheet (SECC, SGCC), copper (CU), brass, purple copper, beryllium copper, aluminum plates (6061, 5052, 1010, 1060, 6063, hard aluminum, etc.), and stainless steel (mirror, brushed surface, matte surface).
According to the different functions of the product and the selection of materials, it is generally necessary to consider the product‘s purpose and cost. The processing process of parts in the sheet metal workshop includes pre product experiments, product processing trial production, and mass production of products. During the product processing and trial production process, it is necessary to communicate and contact customers in a timely manner, obtain corresponding processing feedback, and then proceed with mass production of the product.
Laser drilling skill is an early and practical laser skill in laser data processing. Pulse laser is generally used for laser drilling in sheet metal workshops, with high energy density and short time. It can process small holes of 1 μ m, especially suitable for processing small holes with certain viewpoints and thin materials. It is also suitable for processing deep small holes and micro holes on parts with high strength, hardness or brittle and soft materials.
Laser can complete the drilling process of the burner components of gas turbines, and the drilling effect can be completed in three dimensions, with a quantity of up to thousands. The materials that can be drilled include stainless steel, nickel chromium iron alloy, and HASTELLOY based alloy. Laser drilling skills are not affected by the mechanical properties of the data, making automation relatively simple.
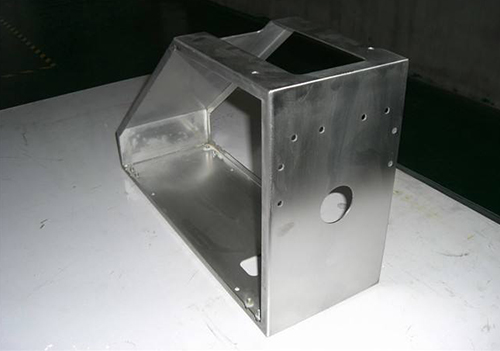