Taking Shenzhen Lida Precision Factory as an example, our production process generally consists of 16 steps, as shown in the following figure.
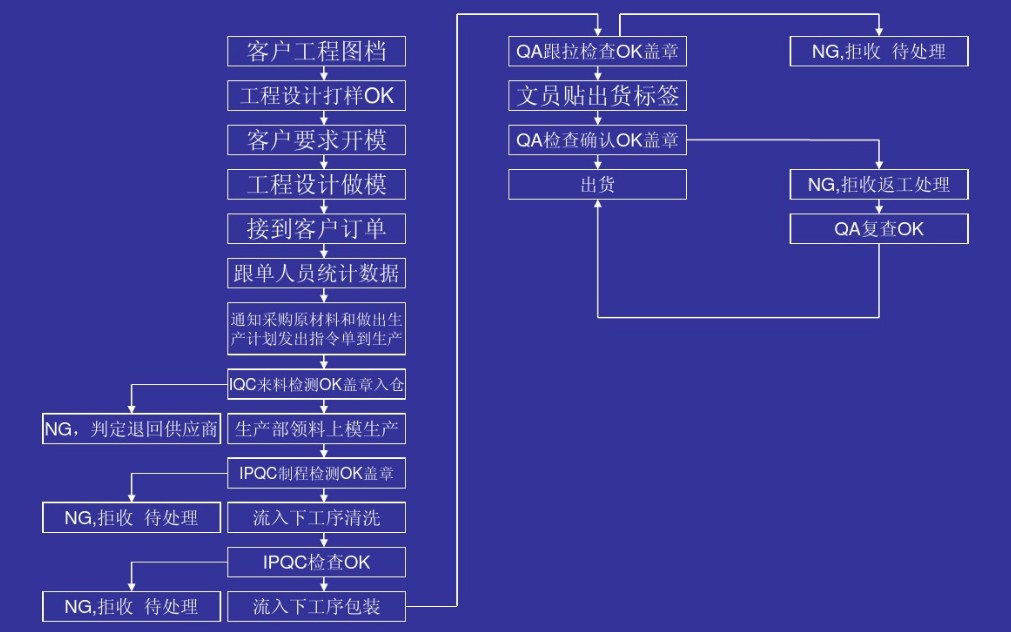
Our main focus of work is:
1、 Production plan: The follow-up department shall promptly confirm the inventory status of raw materials, finished products, etc. in the factory after receiving the order; Whether the technical drawings and material list are in place; Whether the materials can be timely, timely, and in place on time; Arrange the production plan and prepare a copy of the production instruction to be sent to the production department.
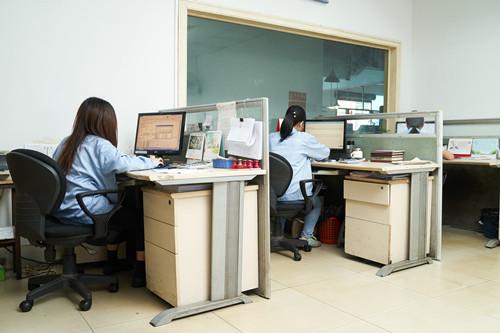
2、 Incoming inspection: To ensure the quality at the source, it is necessary to take a sample of about 1 meter from each roll of raw materials for the following inspection. By visually inspecting and verifying the sample, the material is checked for consistency, and the surface of the material is checked for oxidation, dirt, and other appearance defects. Use a micrometer to check whether the thickness and specifications of the material meet the standards; Each roll is sampled and subjected to reflow soldering to test the material's high temperature resistance (whether there are any defects such as deformation, color difference, oxidation, etc. on the surface after conducting high temperature testing)
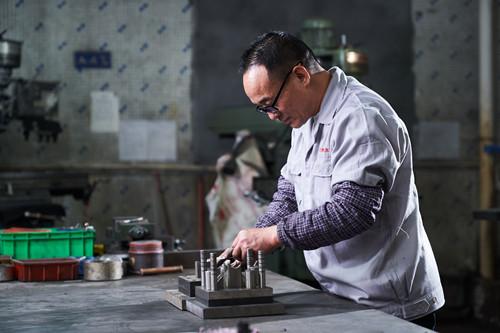
3、 After receiving the production instruction form, the production department produces: materials are collected according to the requirements of the instruction form; Transfer the material into the mold, bend and cut it through several presses, causing the material to deform in the expected design direction of the mold, and shaping the workpiece. The first piece order must be inspected and judged according to all inspection items in the inspection guide book, and the first piece sample must be signed and confirmed before starting production. During the production process, it is necessary to wear finger cots when starting the machine and conduct regular self checks. If any defects are found, the machine should be immediately shut down for improvement.
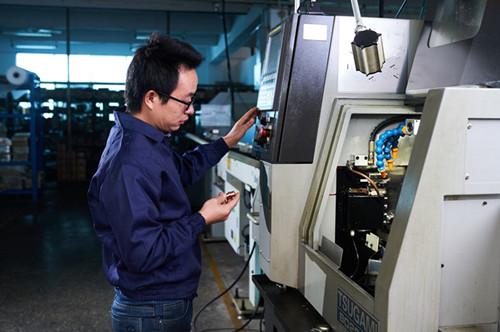
4、 Washing water: At least two cleaning processes. Take out the work in the area to be cleaned and load it into a mesh container. Then, put it into an ultrasonic wave and clean it with carbon and hydrogen for 10 minutes to clean the surface oil stains of the workpiece. After removal, place it in a secondary hydrocarbon cleaning tank and clean it again for 5 minutes to remove any residual sewage on the surface. After taking it out again, place the workpiece in the cleaning tank for 3-5 minutes and filter out the hydrocarbons. During the cleaning process, replace the cleaning agent regularly every 3 hours to ensure the cleaning effect. Then spread out the workpiece and place it on the air drying equipment for about 10 minutes to allow it to air dry completely. Afterwards, place the workpiece into the transfer box.
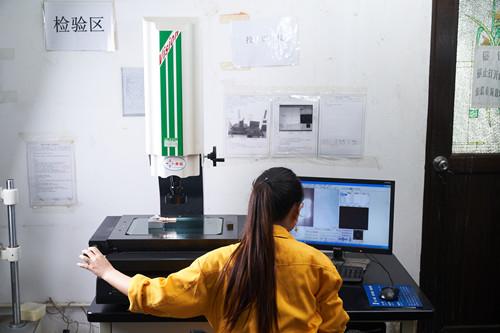
5、 Packaging: Wear finger covers throughout the packaging process and replace them in a timely manner to avoid direct contact between the skin and the workpiece, and to prevent finger marks, dirt, and poor oxidation. The workpieces in the packaging area shall be randomly inspected according to the inspection instructions, and can only be put into packaging after being confirmed to be correct and stamped. Place the packaged workpiece on the packaging table and place it in the tray tray tray in the same direction. Before placing it, self check whether there are any obvious defects on the surface of the workpiece. After confirming the accuracy, the packager affixed the inner box label and sealed the box for shipment.
6、 Confirmation before shipment: The clerk shall affix the shipping label, and QA shall confirm whether the material code on the shipping label is correct, whether it matches the actual product, and whether the quantity is correct. After confirmation, the shipping label must be stamped for confirmation before shipment can be made. If there are any abnormalities, timely rejection and problem feedback shall be made, and modifications and rework shall be made.
Emma Technology Co., Ltd. is one of the leading professional manufacturers of precision metal parts in China, established in 2006. It mainly undertakes business such as CNC Machining parts, metal stamping parts, and sheet metal processing.