The selection of the type of stamping equipment used in a stamping plant should be based on the process nature of the process to be completed, the size of the production batch, the geometric scale and accuracy requirements of the bending parts, etc. Generally, the following principles should be followed:
1. Manufacturers use open crank presses in the production of small and medium-sized and punched parts, bending parts or deep drawing parts.
2. In the production of large, medium and high-precision stamping and bending parts, closed crank presses are often used.
3. In the production of large-scale deep-drawing parts, the use of upload-type closed-type double-action deep-drawing presses is more common. In the production of small and medium-sized deep-drawing parts (especially the deep-drawing forming of aluminum products and enamel products), bottom-driven double-action deep-drawing presses are often used. 4. For the large-scale production of complex-shaped parts, multi-station active presses should be preferred. For the large-scale production of blanking and punching parts, high-speed active presses should be used.
5. Regarding small batch production, especially the production of large thick plate stamping parts, hydraulic presses are mostly used. Mainly used for bending, deep drawing, forming and other processes;
6. Regarding the process of proofreading, bending, and leveling, the press is required to have sufficient rigidity, and a fine press should be selected first. When producing small-scale bending parts, a friction press can be considered. If a crank press is selected to complete the above process, it is necessary to strictly control the closing height of the press and the thickness of the stamping materials to prevent damage to the equipment.
7. Regarding the fine blanking process, it should generally be carried out on a dedicated multi-action fine blanking press. When completing the fine blanking process on an ordinary crank press and a hydraulic press, it is necessary to add a blank holder system and a back pressure system to the equipment or mold.
This article is from EMAR Mold Co., Ltd. For more EMAR related information, please click: www.sjt-ic.com,
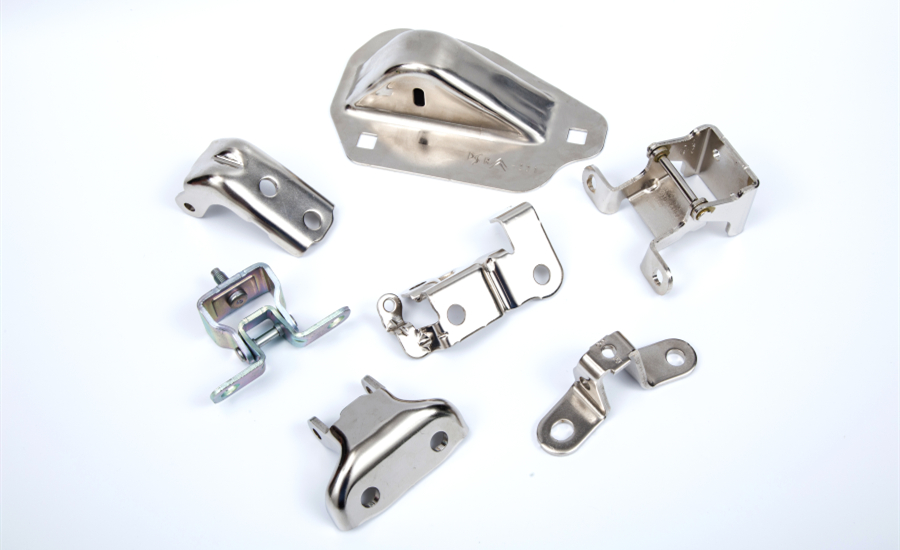