Shenzhen EMAR Precision Technology is a professional manufacturer dedicated to high-precision CNC five-axis machining center external processing. Many users and customers will feel that the five-axis CNC Machining center is a very magical precision equipment. They will also understand its huge energy through some news. In the military field, the five-axis machining center plays a key role (propeller, aero engine and other equipment manufacturing). Today, EMAR Precision Technology has taken stock of some advantages and disadvantages of the five-axis machining center for everyone to share, so that everyone can have a clearer understanding of it. The so-called five-axis machining here refers to at least five coordinate axes (three linear coordinates and two rotary coordinates) on a machine tool, and can be processed simultaneously under the control of a computer numerical control (CNC) system.
A. Rotation around the X axis is the A axis
B. Rotation around the Y axis is the B axis
C. Rotation around the Z axis is the C axis
Introduction of common five-axis machining centers: vertical five-axis machining center, horizontal five-axis machining center
Vertical five-axis machining center, there are two ways to rotate the axis of this type of machining center, one is the table rotation axis. The table set on the bed body can rotate around the X axis, which is defined as the A axis. The A axis generally works from + 30 degrees to -120 degrees. There is also a rotary table in the middle of the table, which rotates around the Z axis in the illustrated position, which is defined as the C axis. The C axis rotates 360 degrees. In this way, through the combination of the A axis and the C axis, the workpiece fixed on the table can be machined by the vertical spindle except for the bottom surface. The minimum division value of the A axis and the C axis is generally 0.001 degrees, so that the workpiece can be subdivided into any angle to process the inclined surface, inclined hole, etc.
Disadvantages: The workbench cannot be designed to be too large, and the load-bearing capacity is also small, especially when the A-axis rotation is greater than or equal to 90 degrees, the workpiece cutting will bring a lot of load-bearing torque to the workbench.
Advantages: The spindle structure is relatively simple, the spindle rigidity is very good, and the manufacturing cost is relatively low.
The other is to rely on the rotation of the vertical spindle head. The front end of the spindle is a rotary head that can rotate 360 degrees around the Z axis to become the C axis. The rotary head also has an A axis that can rotate around the X axis, generally up to 90 degrees or more, to achieve the same function as above.
Disadvantages: The workbench can also be designed to be very large, the fuselage is large, the rotating structure of the spindle is more complex, and the manufacturing cost is also high.
Advantages: The spindle machining is very flexible, and the spindle rotation design is adopted to ensure a certain linear speed, which can improve the surface machining quality. This structure is very popular for high-precision curved surface machining of molds, which is difficult to achieve in worktable rotary machining centers.
Horizontal five-axis machining center, the rotary axis of such machining centers also has two ways, one is the horizontal spindle swing as a rotary axis, plus a rotary axis of the worktable, by the spindle vertical, horizontal conversion with the table indexing, the workpiece to achieve pentahedron processing.
Disadvantages: The spindle has poor rigidity, but it is not linked, making it suitable for different processing requirements of four-axis machining centers with vertical and horizontal conversions.
Advantages: easy and flexible processing, simple replacement of spindle vertical or horizontal rotation, low manufacturing cost, very practical.
The other is the traditional table rotary shaft, and the table A axis set on the bed generally has a working range of + 20 degrees to -100 degrees. There is also a rotary table B axis in the middle of the table, which can rotate 360 degrees in both directions.
Disadvantages: The workbench is limited, the rotating shaft structure is more complex, and the price is also expensive.
Advantages: The rotating shaft can also be equipped with circular grating ruler feedback, and the indexing accuracy can reach a few seconds. It is often used to process complex curved surfaces of large impellers.
Through the above knowledge, have you gained a deeper understanding of the five-axis CNC machining center?
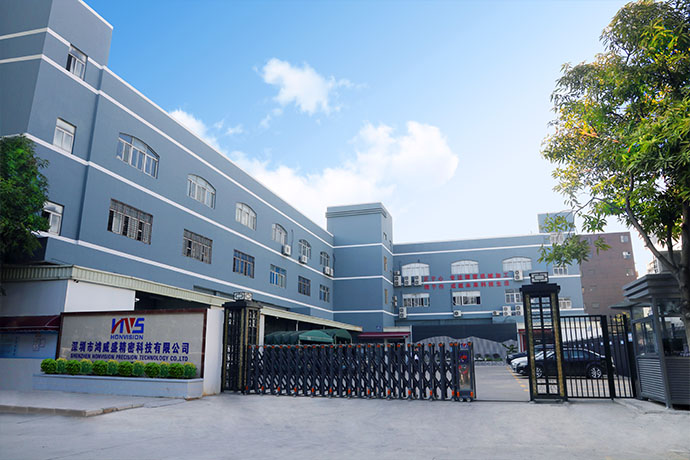