Shenzhen EMAR Precision Technology is a professional dedicated to high-precision optical parts precision machining strength manufacturers, the company is located in our country reform frontier city Shenzhen, after 18 years of development, the company currently has all kinds of precision numerical control processing equipment more than 100 sets, mainly including numerical control centering machine, numerical control cutting machine, turning and milling composite machining center and numerical control milling machine, EMAR Precision Technology based on its own years of optical parts precision machining and reading and summarizing a lot of information, to share with you about laser fusion optical parts processing technology sharing:
At present, the laser fusion device being developed in our country requires a large number of high-precision and large-diameter optical components, and requires timely and quality assurance to manufacture these optical components. It is necessary to break through the existing technological level, adopt efficient and advanced optical manufacturing technology, learn from the experience of ignition devices (NationalIgnitionFacility, NIF) in relevant foreign countries, and combine the actual situation of our country to apply precision machining technology to the precision manufacturing ranks of laser fusion optical components.
Precision Machining of Large Aperture Planar Optical Elements
Most of the optical components in the laser fusion device were rectangular, square, and other polygonal shapes. Compared with the circular components, these components and tools had obvious edge effects (especially in terms of angle). According to the current technical level, it was still difficult to achieve the transmission wavefront (P-V value PeaktoValley, and peak-to-trough value lambda/6) and reflection wavefront (P-V value lambda/4) required by the project. A large number of experiments have shown that the production efficiency of the point solution online correction grinding method (WlectrolyticIn-ProcessDressing, ELID) is significantly higher than that of the traditional grinding process, which is likely to replace the traditional rough machining before polishing - milling and rough polishing, the only drawback is that the accuracy is slightly lower (compared with precision polishing).
Using a gadget numerical control to polish a 340mm * 340mm * 60mm flat mirror, the initial reflected wavefront error is 3.5 lambda (P-V value, lambda = 0.6328um). After polishing for only 30H, the reflected wavefront error P-V will reach 0.26 lambda, and the root mean square value is 0.035 lambda. Just as shown in the drawing (the "+, -" values listed in the ruler in the figure should be expressed in different colors, and the black and white photo is just a schematic diagram). From the figure, it is not difficult to see what is commonly referred to as the "broken band" error. In a strong laser system, this high-frequency error must be strictly controlled, so this process method cannot be used as the final processing of the optical components of a strong laser system.
During the experiment, we found that the accuracy of large-diameter optical components processed by continuous polishing technology can meet the requirements of engineering, but the problem is that the processing cycle is long and the dependence on humans is too strong.
The above technologies all have their own advantages and disadvantages, and none of them can meet the needs of the project alone. The reasonable combination of these technologies can give full play to their respective advantages and meet the specific requirements of the project. The specific idea is to first use ELID grinding technology to precision grind the optical element blank to within 1 lambda, and then use numerical control processing equipment to correct local errors, process the optical element to the surface accuracy required by the project, and finally use a large ring polishing machine to precision polish the optical element to the actual requirements. This process mainly solves the problem of surface roughness and ripple.
After the detailed explanation of EMAR Precision Technology, do you have a deeper understanding of the technology of laser fusion optical parts processing? EMAR Precision Technology focuses on the precision processing of optical parts. We have modern numerical control processing equipment and supporting quality inspection equipment and technicians to provide you with complete product solutions. Welcome to inquire.
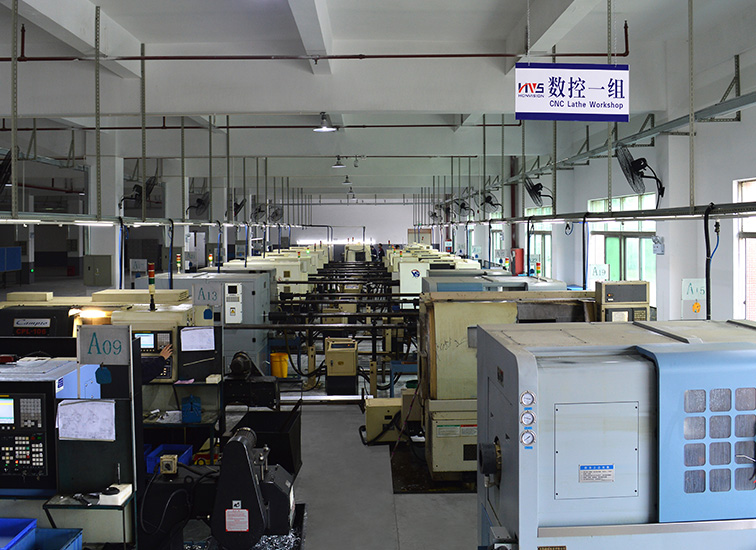