Summary of mechanical processing procedures and price estimation
1、 Mechanical processing steps:
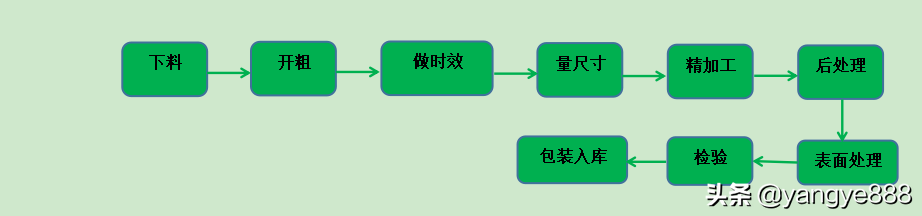
1) Cutting: Use a saw to cut the corresponding material into the approximate dimensions of the parts to be processed. (Generally, leave a margin of 5-8mm for length and width)
2) Rough machining: Using equipment such as lathes, milling machines, and wire cutting to process the rough shape of the parts required by the drawing, removing most of the blank allowance.
3) Time efficiency: Time efficiency is divided into natural time efficiency and artificial time efficiency. Natural aging refers to allowing the workpiece to stand for 24 hours or longer, while artificial aging refers to heat treatment of the workpiece in a high-temperature box or box furnace. The purpose of aging is to eliminate stress and reduce deformation of the workpiece during precision milling process.
4) Measurement size: After aging, the workpiece will undergo some degree of deformation, and it is necessary to re measure the size to determine the margin.
5) Precision machining: Strictly follow the dimensions required by the drawing for precision machining to meet the dimensions of the workpiece required by the drawing. For workpieces with high precision requirements, semi precision machining processes will be arranged as needed before precision machining.
6) Post processing: This process will be interspersed into the previous process depending on the type of part.
1. Fitter: including chiseling, sawing, filing, correcting, drilling, threading, removing burrs, chamfering, and installing screws on workpieces.
2. Grinding machine: When high precision is required for the outer circle, inner hole, and end face of the workpiece, it is necessary to leave a margin after the precision machining process and use a grinding machine for grinding.
3. Boring machine: For holes that require high precision in size, shape, and position, use a boring machine for processing.
4. Testing: Surface testing is required for both screw standard parts and welded parts to ensure the strength of the workpiece.
7) Surface treatment: After the completion of workpiece processing, surface treatments such as ordinary oxidation, pulse anodizing, hard oxidation, passivation, sandblasting, painting, etc. need to be applied to the workpiece surface to achieve aesthetic and anti oxidation effects.
8) Inspection: It is necessary to inspect the surface treated workpiece, including key information such as various sizes and colors, to ensure compliance with the drawing requirements.
9) Packaging and storage: Package the inspected workpieces and store them together with the certificate of conformity, inspection report, and other documents.
2、 Composition of quotation for machined workpieces
1) Materials: Calculate material costs based on the density and price of materials required for different workpieces. ( ρ= M/v)
2) Working hours: mainly including manual operation hours and equipment processing hours, the price is calculated based on personnel hourly wages and equipment hourly fees * program running time. (Programming)
3) Surface treatment fee: The price is calculated based on the different surface treatment processes required by the workpiece drawing.
4) Profit: According to the company's operation and scale, calculate the profit quotation proportionally based on the aforementioned prices.
5) Tax: Accounting for taxes based on the invoicing format and tax points required by the country.
6) Transportation: Corresponding fees will be charged based on different transportation methods. (Examples include air freight, logistics, express delivery, etc.)
3、 Process working hours
The time required to complete a process, process hours=preparation hours+basic time
Preparation time refers to the time consumed by workers to familiarize themselves with process documents, receive blanks, install fixtures, adjust machine tools, align zero positions, and disassemble fixtures.
Basic time is the time taken to process a process program.
4、 Quotation cost estimation method (this method is applicable to mass-produced products for reference)
Processing cost=(material cost+processing fee) * 1.2~1.5 (including management fee, sample and small batch coefficients * 3~5)
Material cost=weight (density * volume) * unit price (yuan/kg)
Processing fee=process hours * unit price (yuan/hour)
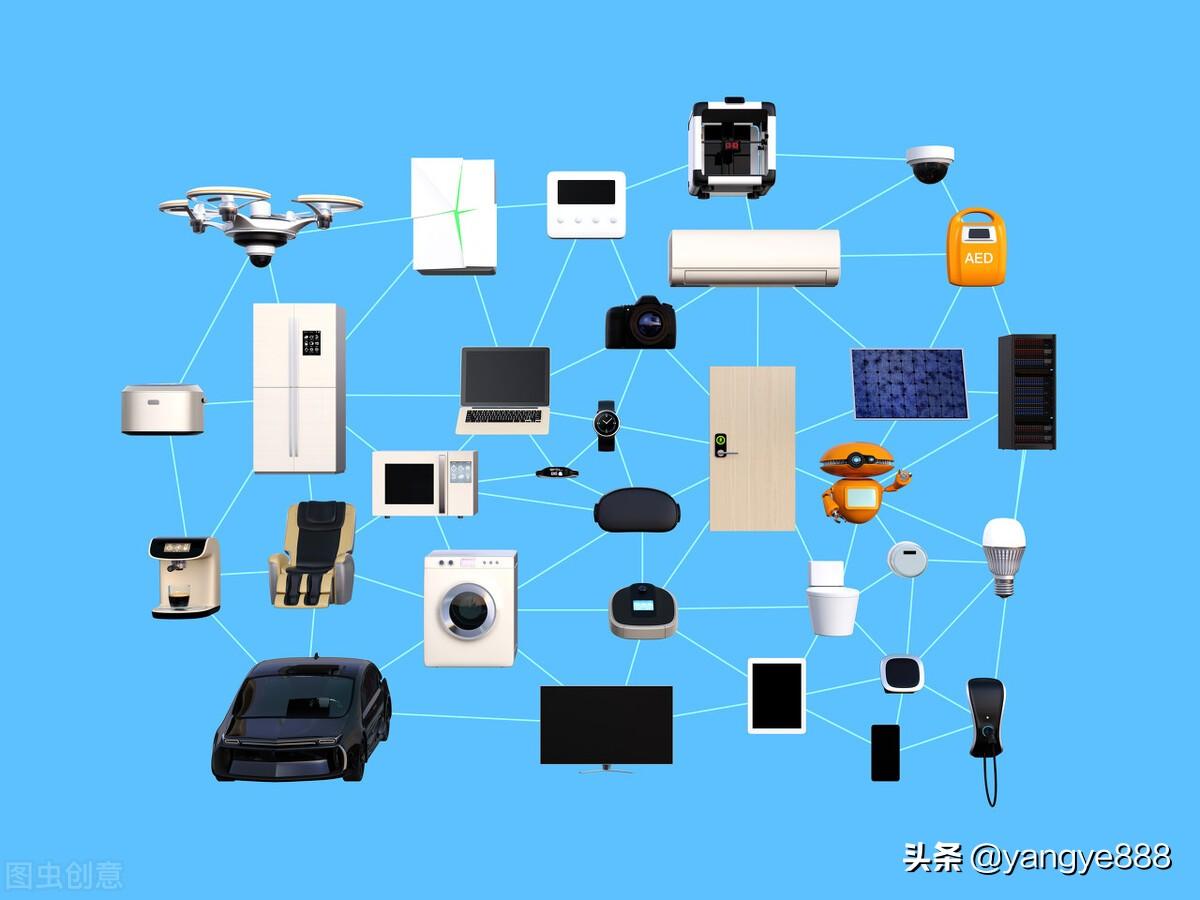
5、 Common aluminum and steel prices:
According to the manufacturer's announcement
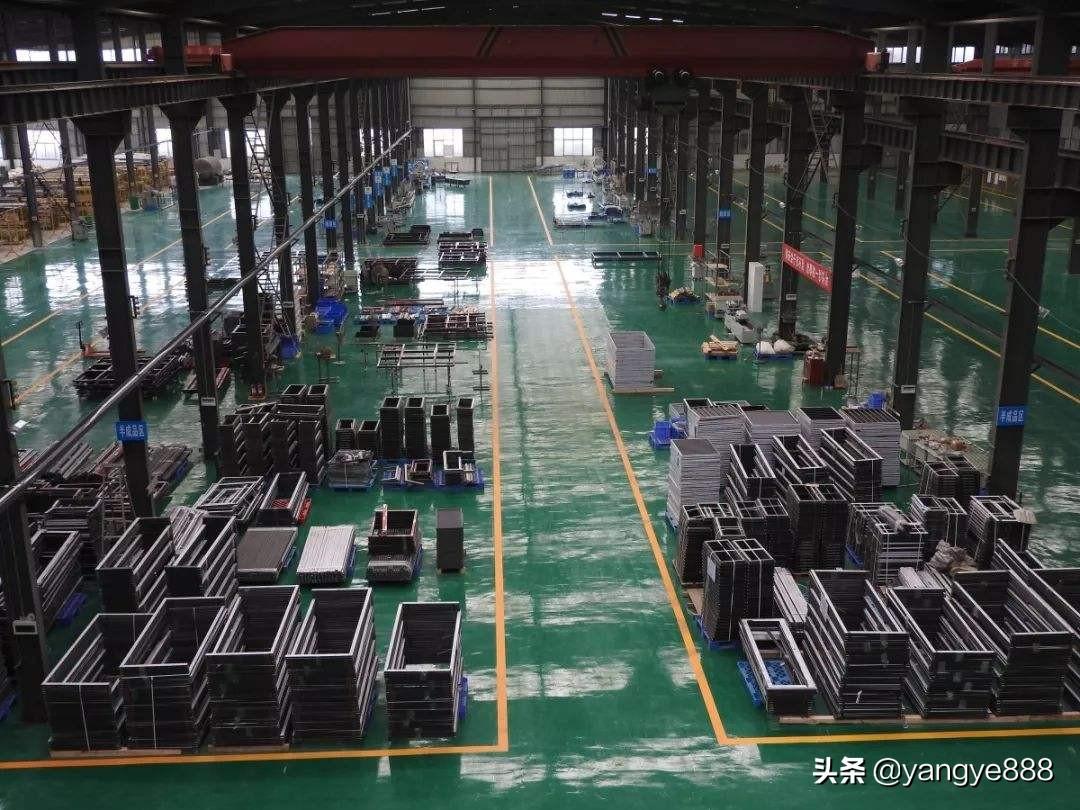
8、 3D printing fee model
Usually charged based on the weight of the materials used (yuan/g) (additional fees will be charged if other treatments are required)
The prices of commonly used materials are as follows:
9、 Welding:
1) Welding rod welding: mainly used for welding between iron and iron. The oxide layer on the surface of the welding rod can be used to isolate air and protect the weld bead.
2) Second protection welding: using carbon dioxide as a shielding gas to protect the welding pass, with a thicker welding layer.
3) Argon arc welding: The most widely used welding method, which uses argon gas as a shielding gas to protect the welding pass. The welding temperature is high, and the welding layer is thin and firm. Can be used for welding of steel, aluminum, and titanium alloys.
4) Laser welding: Laser high-temperature dissolution welding wire with weak firmness, mainly used for welding decorative parts.
5) Vacuum welding: In a vacuum environment, argon arc welding is used to weld, ensuring that the weld bead and workpiece are isolated from air and welding is reliable. The main method for welding titanium alloys.