What is a sheet metal part? Sheet metal parts are a comprehensive cold working process for metal sheets (usually less than 6mm), which includes cutting, punching/cutting/composite, folding, welding, riveting, splicing, and forming to produce components
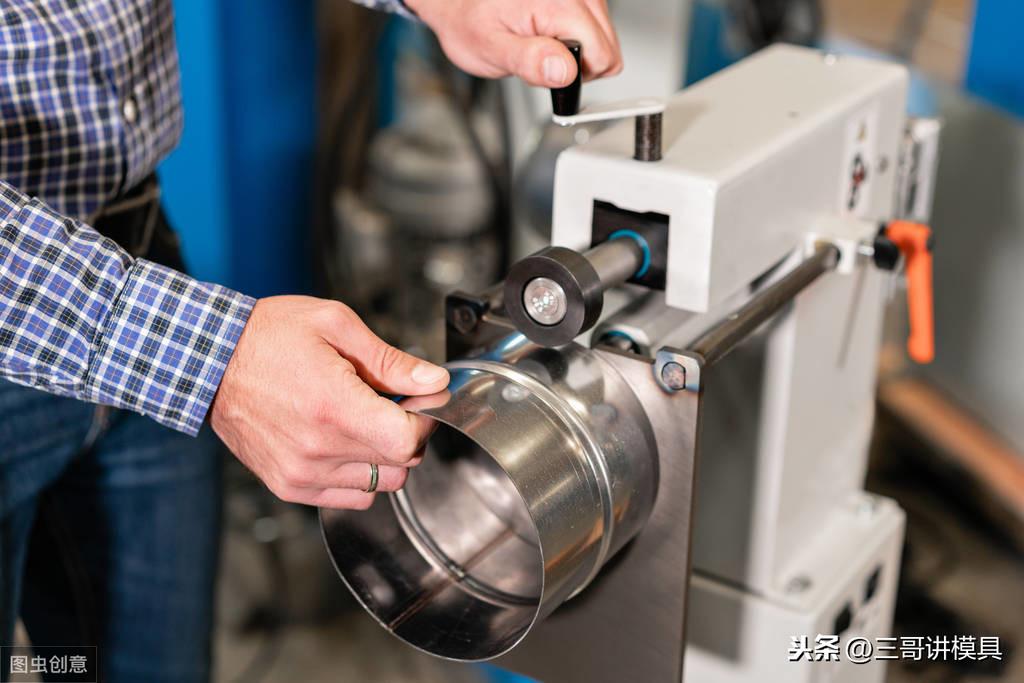
Features:
1. Uniform thickness. For a part, the thickness of all parts is consistent
2. Light weight, high strength, conductivity, low cost, and good performance in large-scale production
Processing technology
1. Cutting
The equipment used in the shearing process is a shearing machine, which can cut a metal sheet into a basic shape. Its advantages include low processing cost; Disadvantages: The accuracy is average, there are burrs in the cutting, and the cutting shape is single, all of which are simple rectangles or other simple shapes composed of straight lines.
Before cutting, it is necessary to calculate the unfolded size of the parts. The unfolded size is related to the bending radius, bending angle, sheet material, and sheet thickness.
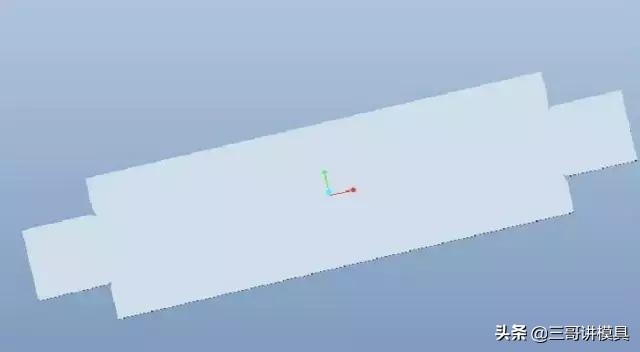
2. Rush
The equipment for punching process is a punching machine, which can further process and shape the cut material. Stamping various shapes requires different molds, common molds include round holes, elongated holes, and protrusions; High accuracy.
Boss: The material should not be removed, and the height of the boss is limited, which is related to the material of the board, the thickness of the board, and the angle of the boss slope.
There are many types of protrusions, including heat dissipation holes, installation holes, etc. Due to the influence of bending, the distance between the edge of the design hole and the edge of the board and the bending edge will be limited
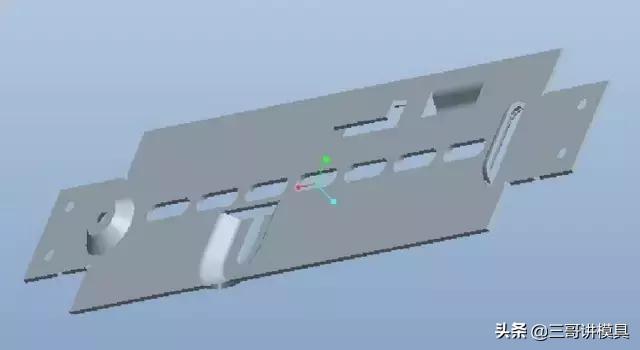
3. Laser cutting
Processing equipment: laser cutting machine
For materials that cannot be removed by cutting or punching processes, or for plates with high hardness that are prone to damaging the mold, such as those with rounded corners, or when there is no ready-made mold to stamp the required shape, laser cutting can be used to complete the forming of the material before bending
Advantages: Cutting without burrs, high precision, capable of cutting any shape, such as leaves, flowers, etc; Disadvantage: High process cost
4. Bending
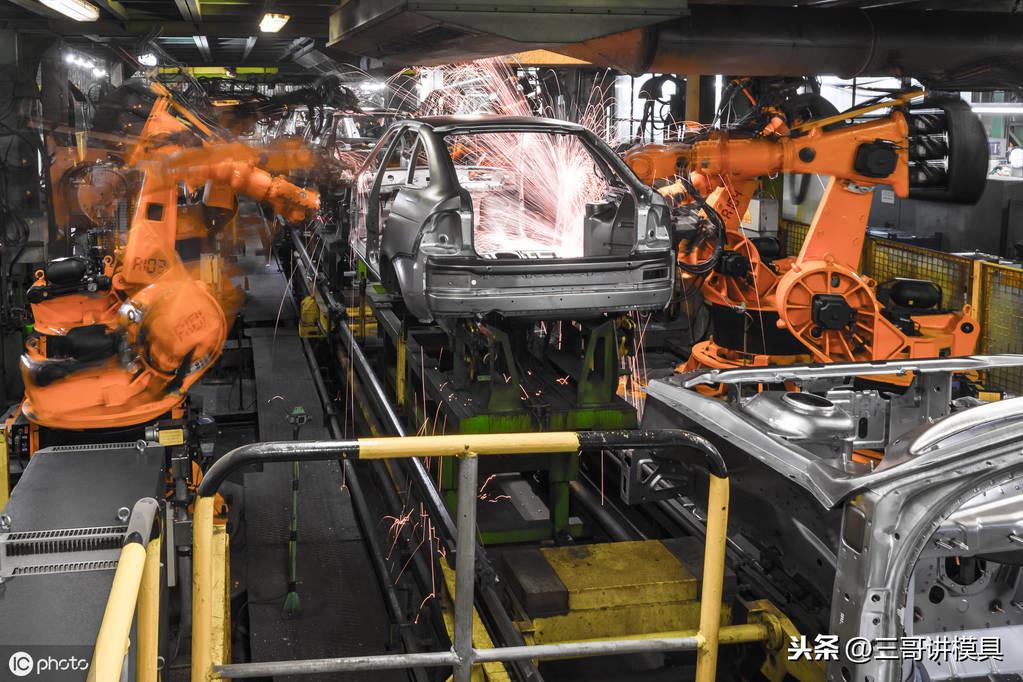
Processing equipment: bending machine, rolling machine
They can fold or roll metal sheets into the desired shape, which is the forming process of components; The process of forming the desired shape by cold pressing a metal sheet with the upper and lower blades of a bending machine is called bending.
Bending is the final step in forming sheet metal parts, and there are several points to pay attention to when the parts can be unfolded and bent into shape. Below, the editor will explain them to everyone.
1. Material shortage, as shown in the figure below. The protrusion is too high and exceeds the ductility of the material. The protrusion is generally used to increase the installation size or avoid installation conflicts. Therefore, the protrusion must be made without changing the internal structure of the material and affecting the structural strength. For example, the angle between the convex cone and the reference plane is 45, and the height is 3 times the thickness of the plate
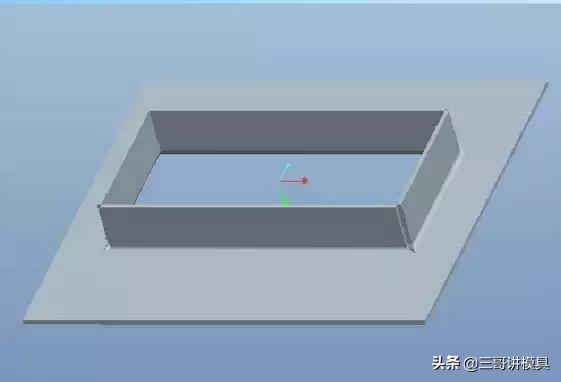
2. Redundant materials: Redundant materials often have multiple closed bending edges, which are often caused by process errors or drawing errors
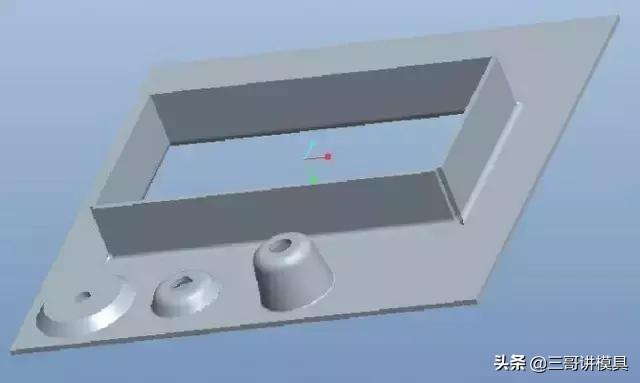
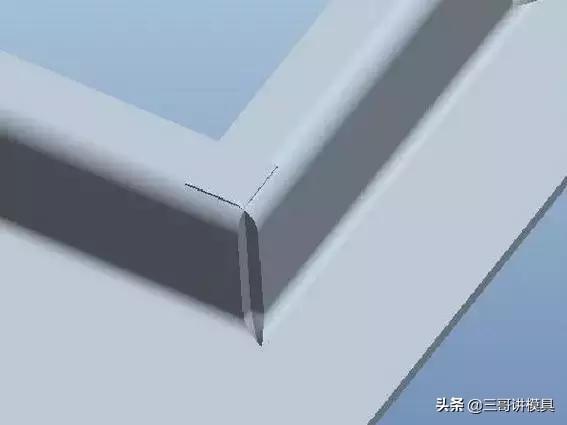
3. Bending restrictions: Most bending machines have certain limitations on bending
Unilateral height: The size of the bending machine and the height of the cutting edge can be determined by using a multi sided large angle bending method
Bilateral height: not greater than the maximum height of one side. In addition to all restrictions on the height of one side, it is also limited by the bottom edge: bending height 4. As sheet metal parts are formed by bending a thin metal sheet, the contact between the bent edges is not sealed and there is no rigid connection. If not treated, it will affect the strength. The usual treatment method is welding. The technical requirements on the drawing include: welding angle, welding angle, and rounding 5. Surface treatment Due to the thin thickness of sheet metal parts, they are not suitable for hot-dip galvanizing. Common surface treatment methods include phosphating and electrostatic spraying, and the color varies with the project. This process is suitable for black parts with untreated surface Alright, that's all for the sheet metal parts and some of their processing techniques. Have you all learned about them? If you have any questions, please say them in the comments section below. Let's communicate and discuss together!