Are you amazed by the molding process of the Zhangqiu iron pot in "Tongue 3", where hundreds or even thousands of blows make the red iron pieces thin and strong. Do you know that the wing panels that make up two wings on the large airplanes we often ride on are also manufactured using similar processing techniques.
Of course, this high-end process, known as "shot peening technology," is much more complex than the production techniques of Zhangqiu iron pots. The common feature of both is to enhance fatigue resistance and increase strength through high-speed impact. The difference is that the hammer has become a small projectile with a diameter of no more than one centimeter, and the iron metal has become a more excellent alloy raw material. The finished product is a large wing wall panel with extremely high toughness and strength requirements, and a very complex shape.
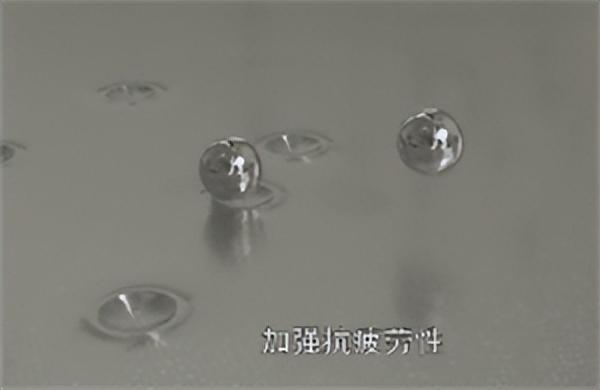
Such thick alloy raw materials, under the high-frequency and high-speed impact of hundreds or thousands of projectiles, become hard, complex in shape, and very thin skin. Finally, they are combined with the skeleton to form a complete wing, supporting the aircraft to fly at an altitude of tens of thousands of meters. Isn't this amazing?
So why do we use shot peening technology to process wing panels? Firstly, we need to understand the special component of aircraft wing panels.
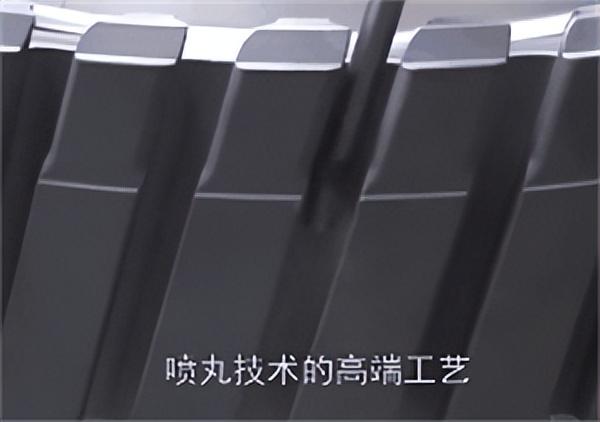
Aircraft wings are a typical thin-walled structure, mainly composed of skin and skeleton. If we compare an airplane to a bird, the skin is like feathers, wrapping around the skeleton of the airplane, forming a streamlined outer surface. It must have a smooth shape to reduce resistance; It must be very light and thin, reaching tens or even a few millimeters, in order to effectively carry weight and lift the aircraft higher; It must also be very resilient to withstand the various maneuvers and twists made by the aircraft at high altitudes.
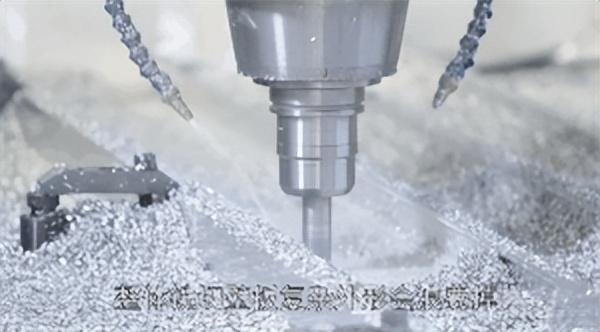
Traditional machining of wing wall panels usually uses CNC integral milling and appropriate mechanical bending methods. Milling the complex shape of the overall wall panel will waste a large amount of material, and mechanical bending can easily affect the performance of the wall panel, making quality control difficult. Nowadays, both domestic and foreign aviation manufacturing companies use shot peening technology for wing wall panel processing.
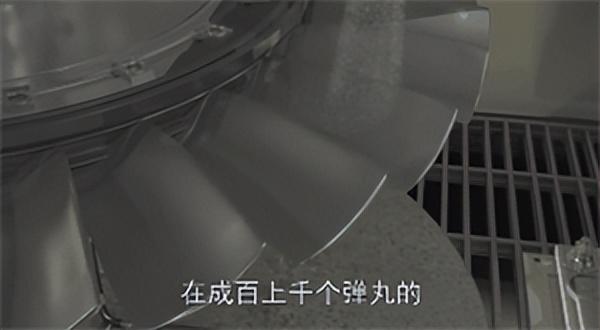
One is low cost, no need for molds, saving raw materials, and occupying less space.
The second is high quality, which continuously "hits" the surface of the parts to become denser, like adding a protective film to the parts.
Thirdly, it has a wide range of applications. No matter how complex the shape is, under computer programs, small projectiles can accurately locate and strike, effectively solving problems such as metal part processing deformation and welding part deformation.
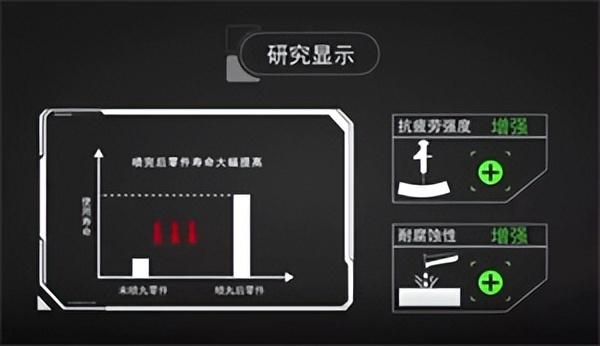
The fatigue life of parts processed by shot peening can be increased by dozens of times compared to the original, and the fatigue strength and corrosion resistance are greatly enhanced.
The medium for shot peening is commonly referred to as shot material, and there are many types, including cutting wire steel shot, carburized steel shot, hard cast steel shot, ceramic shot, and so on. In the field of aircraft manufacturing, shot peening generally uses carburized steel shot and hard cast steel shot, while shot peening strengthening technology mainly uses hard cast steel shot and ceramic shot.
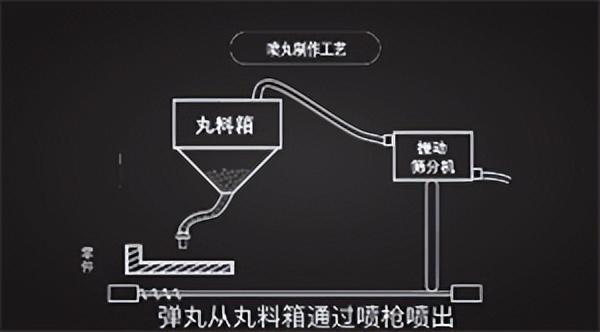
The process of shot peening is very interesting. In a specialized processing equipment, bullets are ejected from the shot material box through a spray gun, hitting the surface of the parts at high speed. Then, through a recycling system, unqualified bullets are screened out by a screening device and returned to the shot material box for reuse.
In order to give domestically produced aircraft stronger and lighter wings, Chinese aviation industry technology personnel are still working hard. More advanced technologies such as prestressed shot peening, ultrasonic shot peening, high-pressure water shot peening, and laser shock shot peening are bound to play a greater role in the near future.