Cars and gears play very important roles in various industries around the world, especially in the automotive industry. It is said that more than half of all gears produced around the world are aimed at the automotive industry.
A large number of gears are used inside the main units of the transmission, differential, control device, and so on.
Gear applications in automobiles
In order to reduce fuel consumption, multi-level transmission is being promoted with a focus on large vehicles. There are many gears installed in a multipole gearbox, and due to the tendency to increase noise, while reducing gear costs, it is also necessary to improve machining accuracy and tooth surface smoothness.
The issue of reducing noise through gears is not only important for gasoline and diesel engines, but also for hybrid and electric vehicles that use gear mechanisms in the driving part.
Complex transmission structure
compound machining machine drives the evolution process of gear machining
In the production of spur gears, the previous gear processing started with machining the gear body on the lathe, followed by gear hobbing with a hobbing machine, chamfering with a chamfering machine, and precision machining with a gear shaving machine before undergoing heat treatment to complete.
The production lines made from these specialized machinery have many advantages in large-scale production, but they are not very suitable for multi variety and small quantity production. In recent years, there has been a trend to transfer production to production lines using general machines such as composite processing machines.
Previous gear machining methods
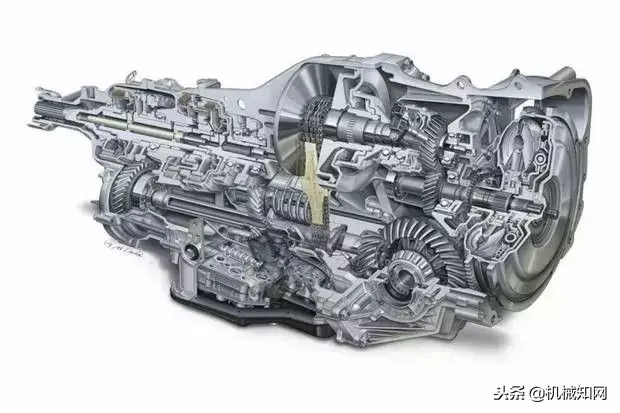
When using a composite machining machine for gear machining, the advantages of CNC lathes and machining centers can be fully utilized. Previously, gear cutting and precision machining were carried out using multiple specialized machines, and all machining processes until heat treatment could be completed using one machine.
Compared with previous production methods, when producing multiple varieties and a small quantity, process intensification can shorten processing time, reduce the number of equipment and machines, and improve processing accuracy.
The gear processing application program for "smooth milling," "smooth hobbing," and "smooth turning" using a composite machining machine completes all processes from basic machining to precision machining of gears through a single clamping process. Especially when processing small batches of gears and large-diameter gears, the production efficiency can be greatly improved.
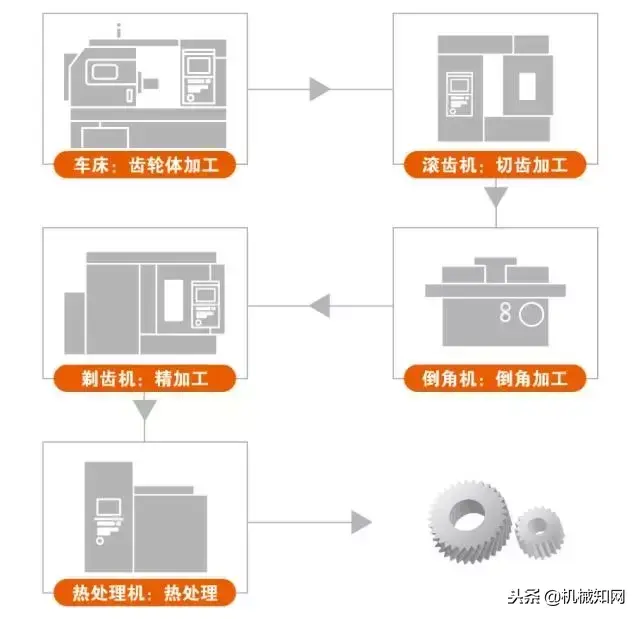