To achieve high-precision and high-efficiency production of customized samples for CNC lathes, we can start from the following aspects:
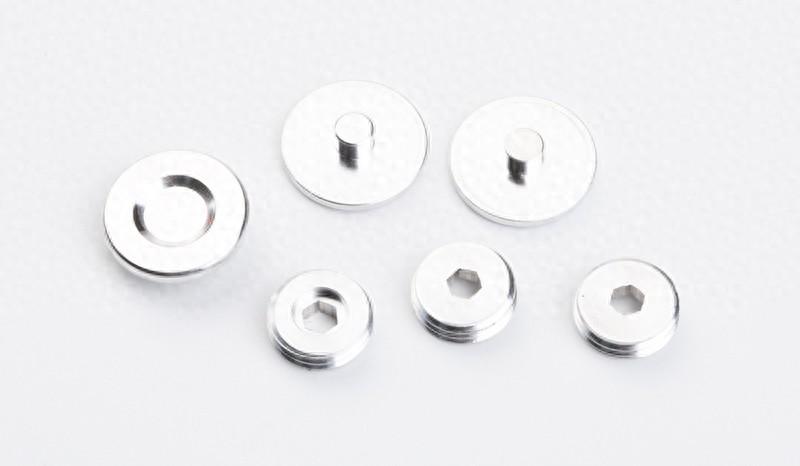
1、 Device selection
Choose high-precision machine tools and cutting tools. High precision machine tools and cutting tools can provide more precise machining and avoid the accumulation of errors.
Choose a CNC lathe with good stability and accuracy to ensure that the accuracy of the machine tool itself can meet production requirements.
2、 Process optimization
In the process planning stage, it is necessary to fully consider factors such as the material, structural characteristics, and geometric tolerance requirements of the parts, and choose a reasonable milling process and a concise processing route.
Optimize the machining sequence and tool path, reduce unnecessary idle travel and tool replacement time, and improve machining efficiency.
Improve machining accuracy through precise positioning reference method. Process a positioning reference surface on the blank first, and directly use the processed surface as the reference to reduce positioning errors.
3、 Parameter adjustment
Reasonably set machine tool parameters, such as system gain and positioning dead zone, to optimize machine tool performance.
Adjust tool parameters such as cutting speed, feed rate, and cutting depth according to different materials and processing requirements to ensure machining quality and efficiency.
4、 Error control
Strictly control the temperature of the spindle box to avoid affecting machining accuracy due to thermal deformation of the spindle. Heat dissipation can be achieved by adding heat sinks or using cutting fluid.
Adopting error compensation technology, reducing errors and improving machining accuracy through hardware compensation and software compensation.
5、 Intelligent management
Introducing an intelligent management system to achieve automated and intelligent production of CNC lathes. Improve production efficiency and machining accuracy through data analysis and optimization algorithms.
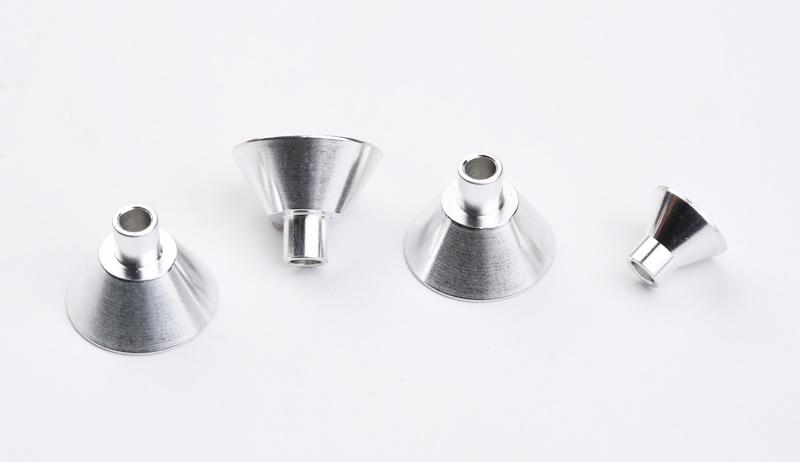
6、 Personnel training
Strengthen the skill training of operators, improve their proficiency in CNC lathe operation and understanding of machining processes.
Regularly organize technical exchanges and training activities, share advanced processing techniques and experiences, and promote the overall skill level improvement of the team.
In summary, achieving high-precision and high-efficiency production of customized samples for CNC lathes requires comprehensive consideration of equipment selection, process optimization, parameter adjustment, error control, intelligent management, and personnel training. By continuously optimizing and improving these aspects, the production efficiency and machining accuracy of CNC lathes can be gradually improved to meet the high-precision requirements of customized sampling.